Injection Mold Tooling
Our Custom Injection Molding Tooling Services
Our injection molding process creates reliable injection molds for your custom injection molded parts. Get accurate and excellent custom injection molds to produce high-quality plastic parts with short cycle times and competitive prices to escort your injection molding projects.
- Advanced Equipment & Cost-Effective Price
- 10+ Years of Injection Molding Tooling
- ISO 9001 & ISO13485 Certified Factory
- Injection Molding Tooling As Fast As 2 Weeks
- Instant Injection Molding Tooling Quotes
- Professional DFM Report
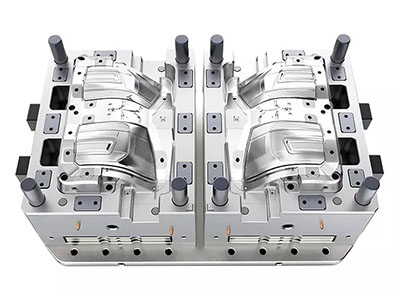
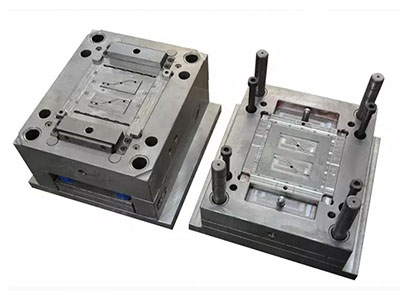
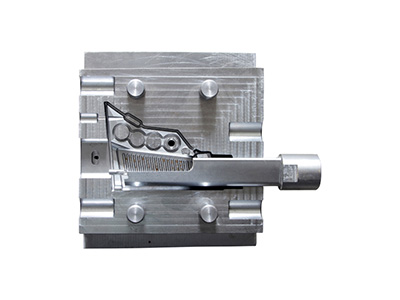
STEP | STP | STL | IGS | IGES | PRT | SLDPRT | SAT | X_T | IPT | CATPART | PDF
Max. file size: ≤20MB
- All uploads are secure and confidential.
Our Robust Injection Mold Making Services
NOBLE is a professional plastic injection mold manufacturer with more than 10 years of experience. From prototype design to production, with refined mold design, selection of appropriate processes, and reduced production costs, you can get stable performance, long life, and high-precision molds in a shorter time. Please upload your CAD file to get an instant quote and let us be your trusted injection mold manufacturer.
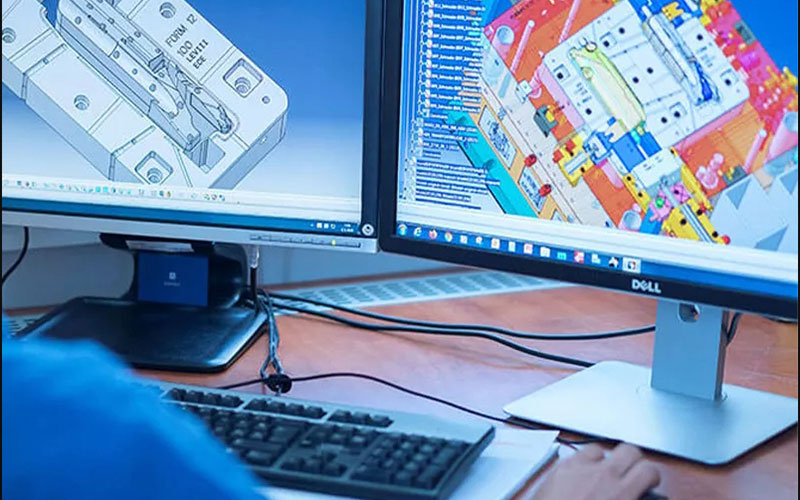
NOBLE has an experienced mold design team that can optimize mold design, select appropriate processes, and reduce manufacturing costs, so that you can get molds that meet your specifications, have stable performance, and have a long life.
- 10+ Years of Experience in Mold Design
- Experienced Team of 100+ Engineers
- 1-to-1 Quote Analysis
- DFM Report and Mold Flow Analysis
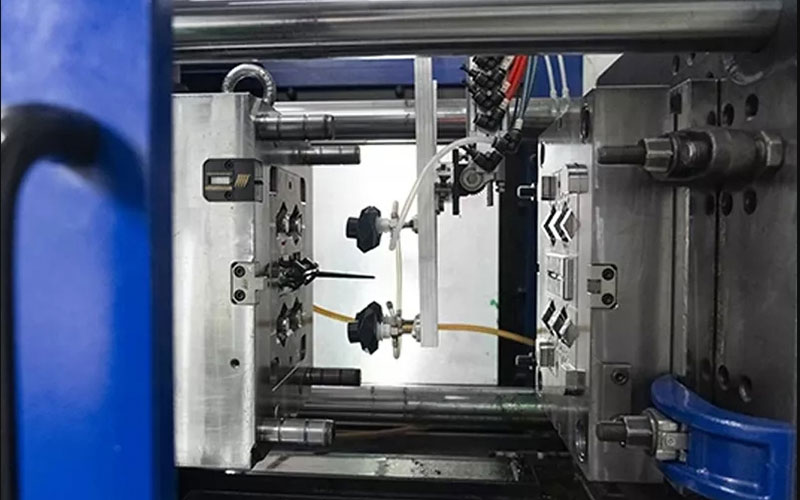
NOBLE’s experienced team of engineers conducts refined design of injection molds, eliminating the waste of excess materials and low output, and reducing the production cost of injection molds.
- Familiar with Internal Mold Construction
- Familiar with HASCO, DME, LKM Mold Standards
- More Than 200 Advanced Precision Machining Equipment
- Precision Tolerance ±0.001mm

NOBLE has a strict quality assurance process to provide high-quality molds with long life, stable performance at competitive prices. Experienced engineers will strictly follow the process to check each mold to ensure that it meets our strict quality standards.
- 3D Solid Modeling
- Fully in-house Mold Design with 100+ Engineers
- Quality without Compromise
- Strict Quality Inspection Process
Our Robust Injection Molding Tooling Capabilities
From Prototyping to Manufacturing
NOBLE is your trusted one-stop injection mold supplier, from prototype design to manufacturing, through the fine design of injection molds, the selection of appropriate processes, and the reduction of production costs, to ensure that you get high-precision injection molds with stable performance and long life in a shorter time.
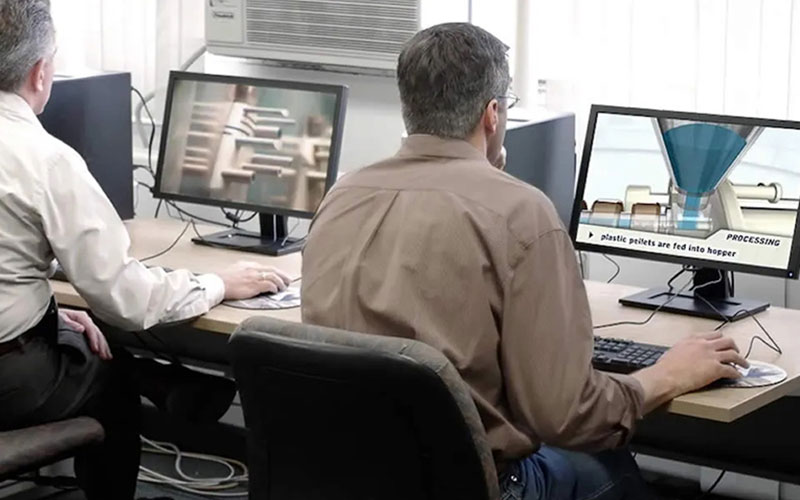
24/7 Engineering Support
From prototyping to production, NOBLE’s experienced engineers provide valuable insights and suggestions to optimize your manufacturing process, allowing you to obtain the highest quality results in the shortest time and at the lowest cost.
- 1-to-1 Quote Analysis
- Satisfied Clients 100%
- Instant Online Quote
- 100+ Experienced Engineering Team
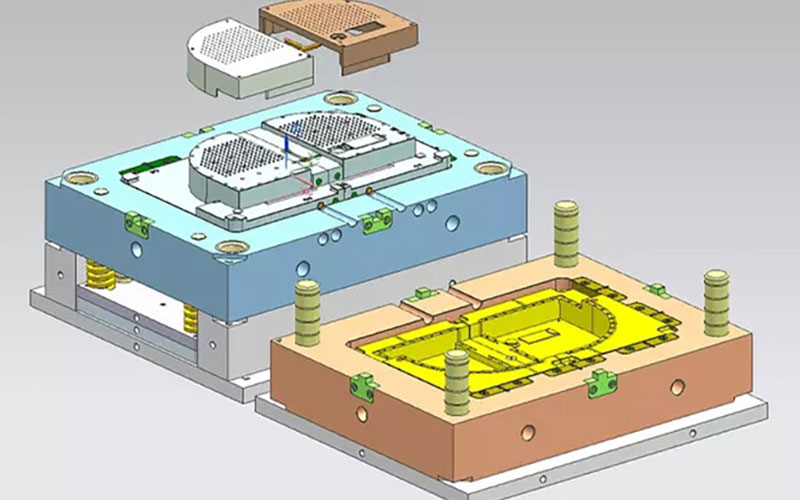
Mold Design & Engineering
Design for Manufacturing (DFM) is a critical point in the injection molding process. Our experienced engineers will optimize your mold design, check your CAD model, identify potential problems, make suggestions, and ensure that you get an economical and long-lasting mold in a short time.
- 10+ Years of Experience
- Provide Free DFM Report in 12 h
- 12+ Years of Experience Engineering Team
- Complete mold design in 2 days
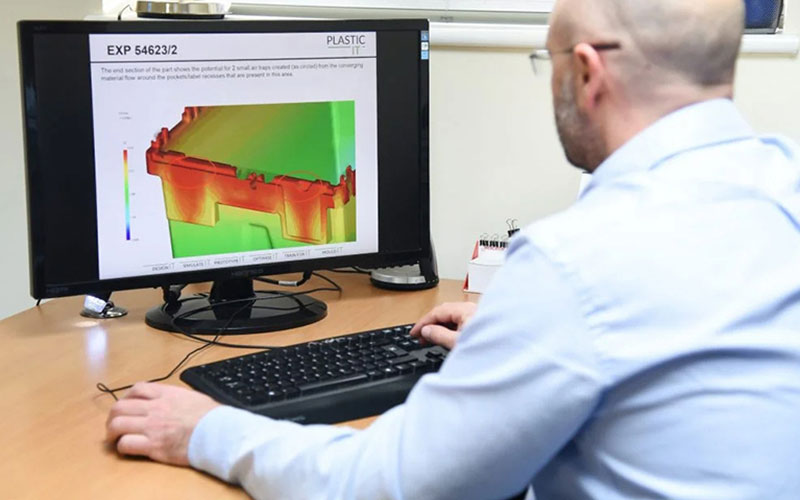
Moldflow Analysis
NOBLE’s Moldflow analysis uses Autodesk’s advanced 3D solid mold filling, cooling, and warpage technology. This allows us to predict and optimize the injection molding process, reduce production costs, and ensure that you get high-quality, high-precision molds in a short time.
- Advanced Analysis and Production Technology
- Advanced Autodesk Solid Modeling
- 10+ Years of Engineering Team
- Free Moldflow Analysis Report
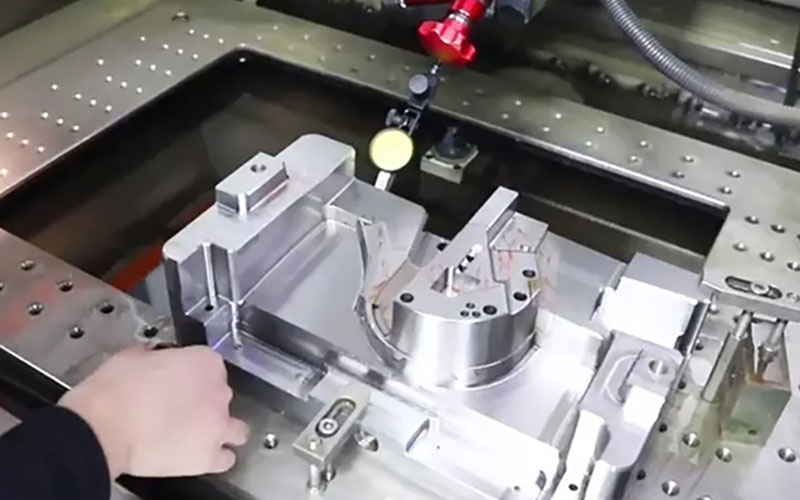
Injection Mold Making
NOBLE is different from other mold manufacturing suppliers. It can quickly find and effectively solve problems during the mold trial process, so that more than 98% of our export molds can successfully pass the mold trial in one try, improve production efficiency, and the mold machining accuracy is as high as 0.001 mm.
- Precision Tolerance ±0.001mm
- 200+ Precision Machining Equipment
- 10+ Years of Engineering Team
- 10+ Years of Experience in Mold-Making
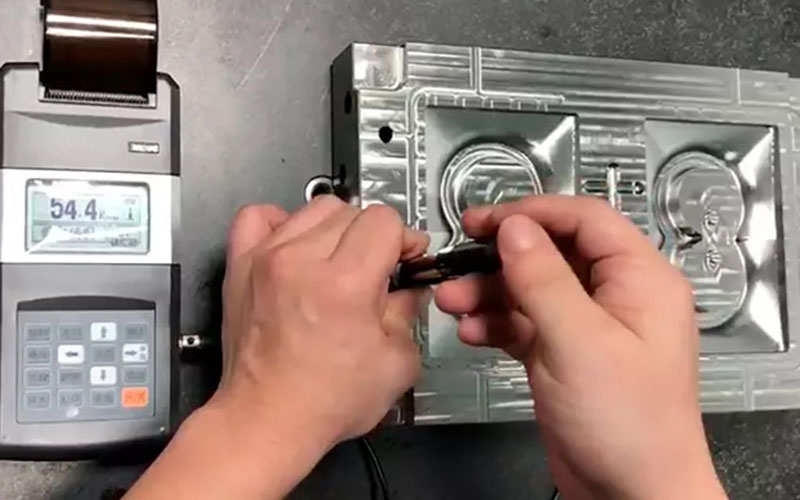
Strict Quality Control
NOBLE has a rigorous quality assurance process in place to ensure that every mold we produce is of the highest quality. Our team inspects every mold thoroughly to ensure that it meets our stringent quality standards.
- Mold Design Control
- Mold Pre-assembly Inspection
- Heat Treatment Hardness Inspection
- Mold Core and Cavity Steel Dimension Inspection
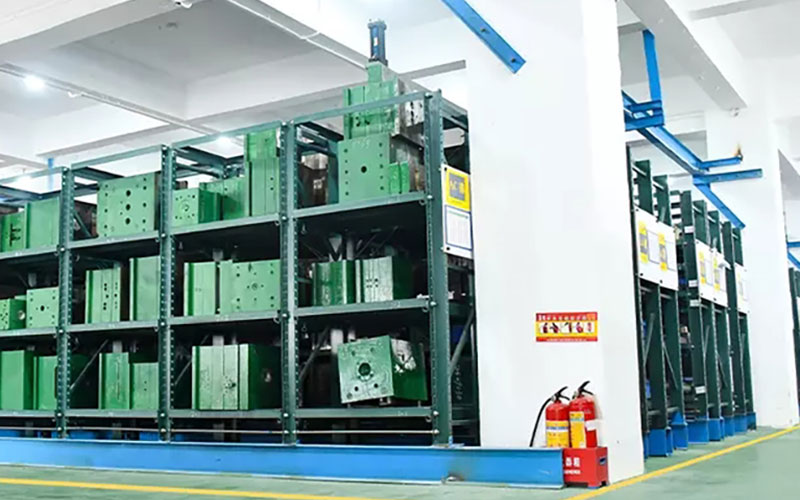
Fast Lead Time
NOBLE will provide weekly accuracy reports and mold progress charts to keep you informed of the progress, strictly including mold quality, provide online mold trial videos, and send samples for confirmation to ensure that your requirements are met.
- Real-Time Weekly Progress Report
- Provide Online Mold Trial Video
- 50+ Countries Shipped
- 99.5% On-time Delivery
From Prototyping to Manufacturing
NOBLE is your trusted one-stop custom manufacturing solution, from prototype design to manufacturing, through huge manufacturing resources, suitable technology, streamlined process, expert guidance, and perfect quality inspection process to turn your ideas into reality.
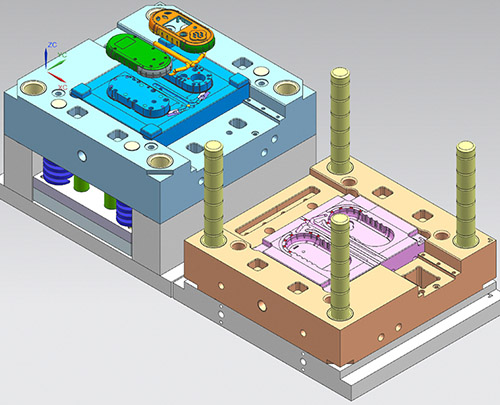
Mold Design & Engineering
Injection mold design is a key element of the injection molding process as it plays an important role in determining the quality and precision of the final injection molded parts. NOBLE has a professional design team to provide you with the best injection mold design solutions.
- 10+ years of Mold Design & Engineering
- State-of-the-Art Equipment
- 1-to-1 Quote Analysis
- Free DFM Feedback
- Strong R & D capability
- Free DFM and Mold Flow Analysis Report
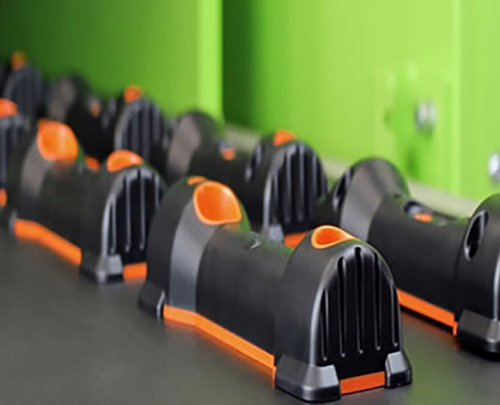
Mold & Prototype Manufacturing
Once the mold design is approved, we begin manufacturing the mold. We then perform prototype injection molding to quickly and efficiently produce and test them for small batch production of plastic parts.
- 10+ Years of Mold & Prototype Manufacturing
- Thousands of resins to choose from
- Competitive & Affordable Price
- State-of-the-art Equipment
- 100% Part Inspection
- Fast Lead Time
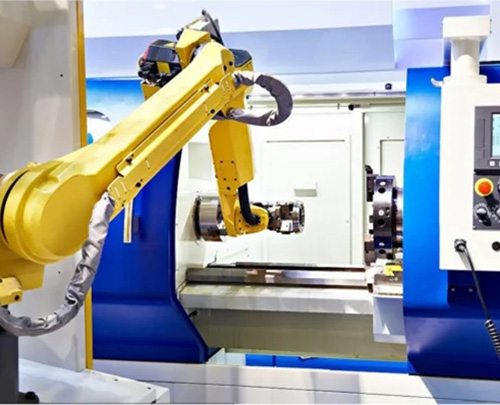
Low-Volume & Medium Injection
NOBLE meets your small and medium batch injection molding needs through strict tolerance control, quality inspection, and complete supply chain, and quickly delivers cost-effective, high-precision parts.
- 10+ Years of Medium & Low Injection Molding
- Competitive & Affordable Price
- State-of-the-art Equipment
- Guaranteed Consistent Quality
- 100% Part Inspection
- Fast Turn-Around Production
Why Choose Us for Custom Custom Injection Molding Tooling Services
Strict quality standards ensure consistency and quality of molded parts. A professional engineering team provides you with technical support from prototyping to production.NOBLE provides customers with high quality and reliable molds.
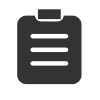
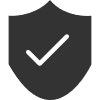
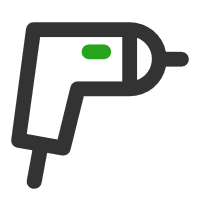
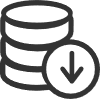
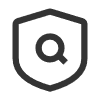
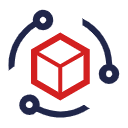
Work with Us in 4 Simple Steps Only
With many years of manufacturing experience, NOBLE offers the best solutions for all rapid prototyping and low-volume manufacturing needs. We streamline the innovation cycle into four simple but effective steps.



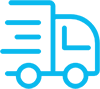
Challenges You May Face in Mold Manufacturing
You receive the mold and find problems such as burn marks, flow lines, air holes, sink marks, undershot, and flash.
Long injection molding cycles and poor communication will lead to increasing mold manufacturing costs.
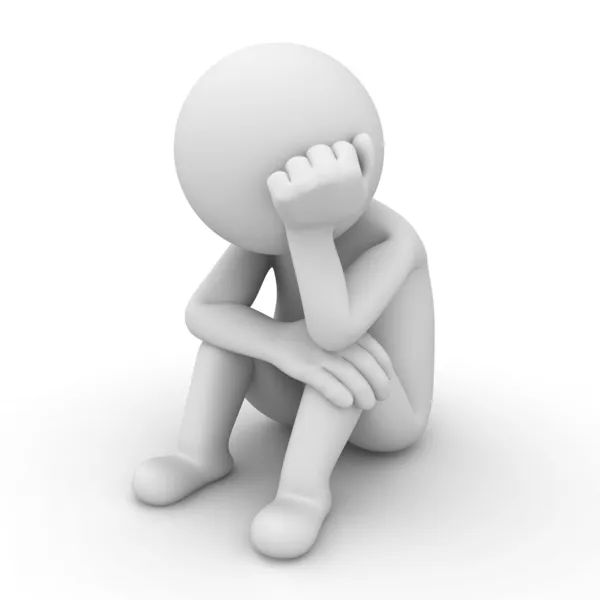
Frequent mold trials and repairs due to mold design or manufacturing process issues often delay project schedules.
Your current mold supplier often gives various reasons, resulting in repeated delays in delivery dates, and affecting the time it takes to launch your products.
How NBOLE Solves Problems in Mold Manufacturing
As a first-class injection mold manufacturer in China, NOBLE is better than other mold manufacturers in that we have an experienced team of engineers, advanced mold manufacturing equipment, active coordination, effective communication, and accurate problem-solving capabilities.
Professional Mold Design
Our experienced engineers will strictly follow international standards in the mold design process. Most molds can be put into mass production after only one trial production.
- Our in-house mold design team consists of 50 engineers with more than 40 years of mold design experience. Equipped with the most advanced software such as Solid Works, we are committed to providing the best and most innovative mold manufacturing solutions.
- We will repeatedly confirm with you to understand the mold function, structure, and precision. We will also provide professional material selection suggestions to help you optimize the design, reduce mold manufacturing costs, and shorten project cycles.
- Provide detailed design for manufacturability (DFM) reports and mold flow analysis to identify potential problems, complete mold design within 1-3 days, and provide 3D mold drawings for your confirmation.
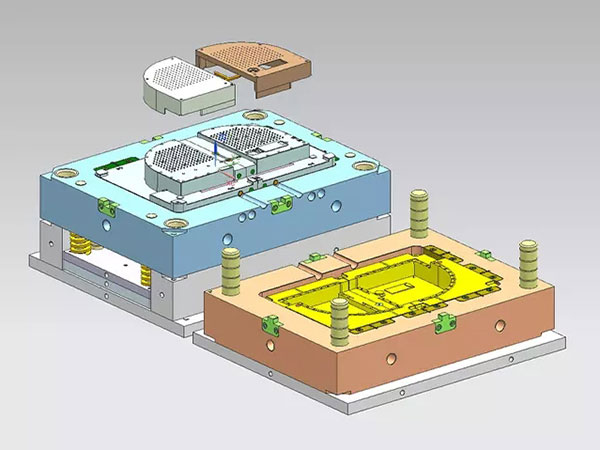
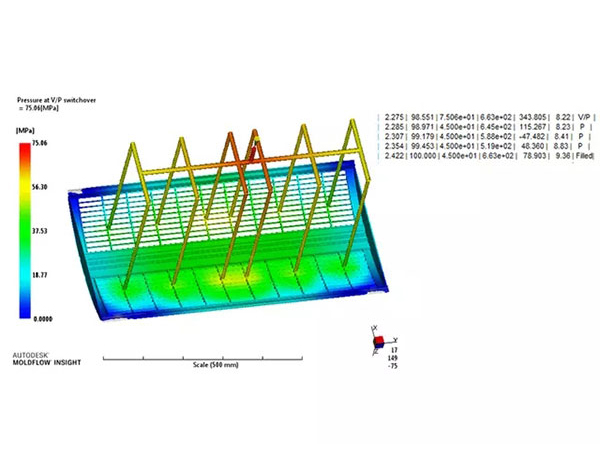
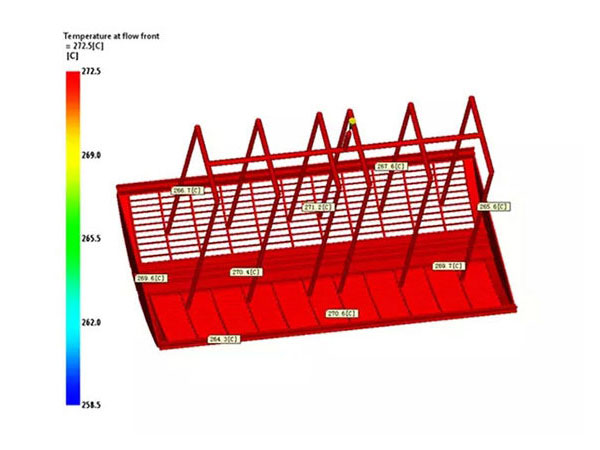
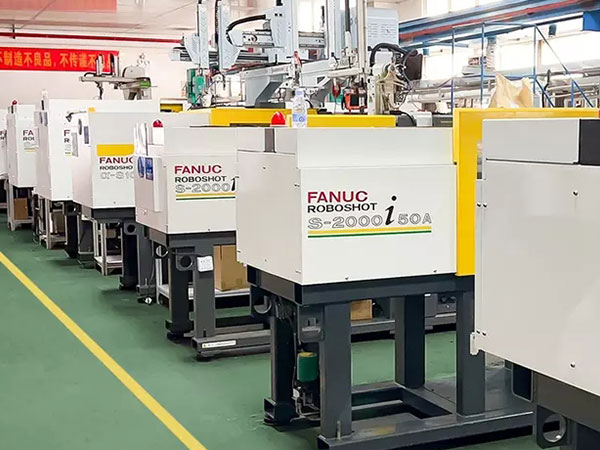
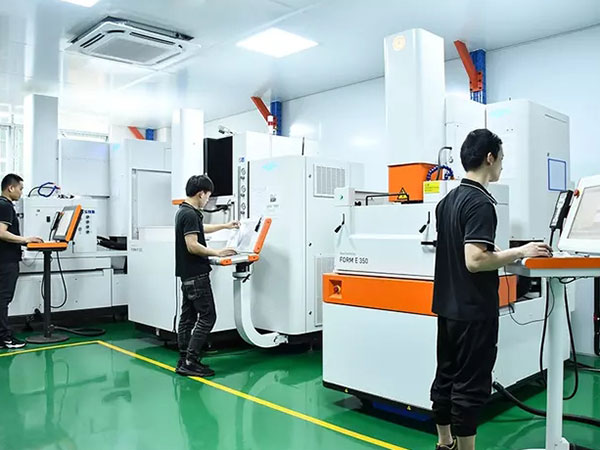
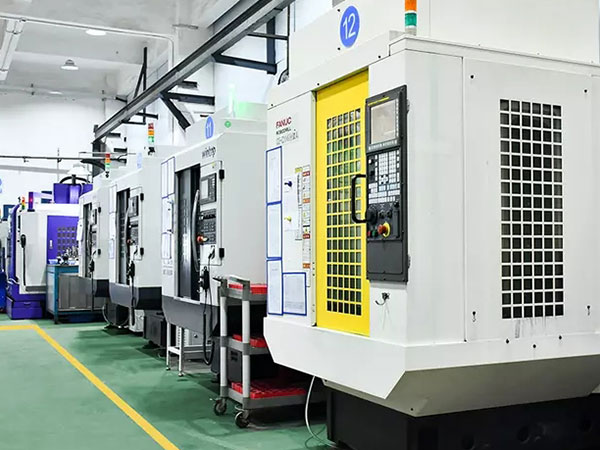
Powerful Mold Manufacturing
We have the most advanced mold processing equipment and an experienced engineering team, with an accuracy of up to 0.001mm.
- We produce more than 5,000 sets of molds each year, following industry standards such as HASCO, DME, and LKM. Our molds are mainly exported to more than 200 countries and regions around the world
- We have imported more than 500 high-precision manufacturing equipment from Switzerland, Germany, and Japan, including high-speed CNC machines, Charmilles mirror EDM machines, wire cutting machines, Zeiss CMM machines, etc., to ensure that mold accuracy can reach 0.001mm.
- Our mold trial technicians have more than 40 years of industry experience and can quickly discover and effectively solve problems during the mold trial process, allowing more than 98% of our export molds to successfully pass the mold trial at one time, reducing downtime and improving production efficiency.
Strict Quality Inspection
NOBLE conducts strict quality inspection on each exported mold to ensure that you receive molds and parts that far exceed your expectations.
- Mold Steel Hardness Inspection
- Heat Treatment Hardness Inspection
- Mold Trial Report and Sample Inspection
- Mold Core and Cavity Steel Dimension Inspection
- Mold Pre-Assembly Inspection
- Final Inspection Before Shipment
- Export Mold Packaging Inspection
- Mold Electrodes Inspection
- Mold Design Control
- Fixture Inspect
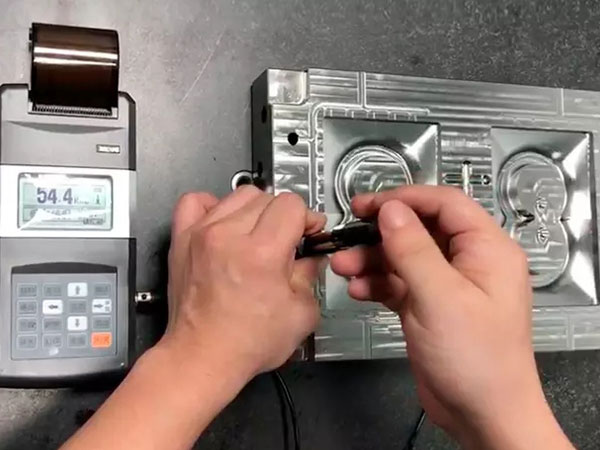
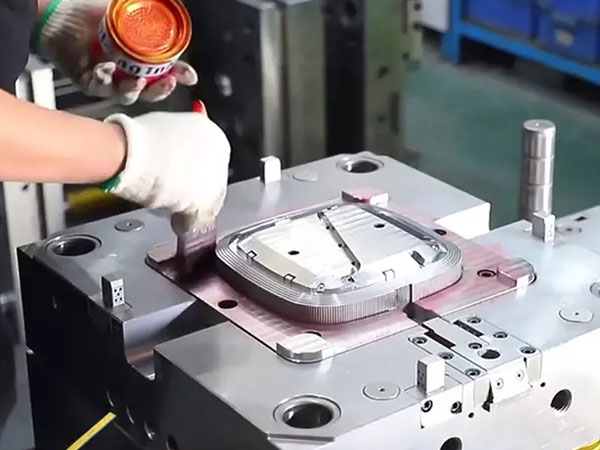
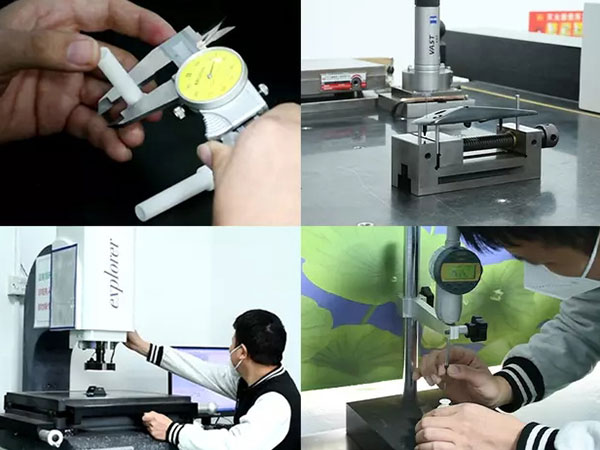
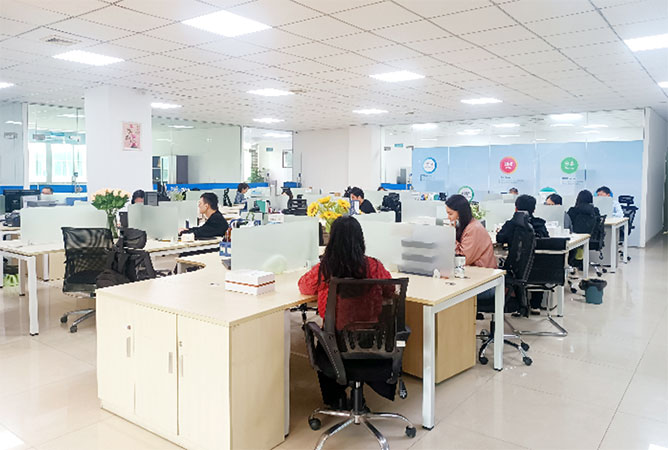
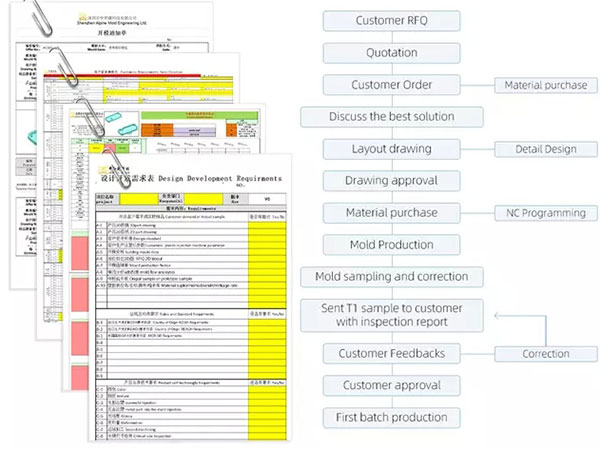
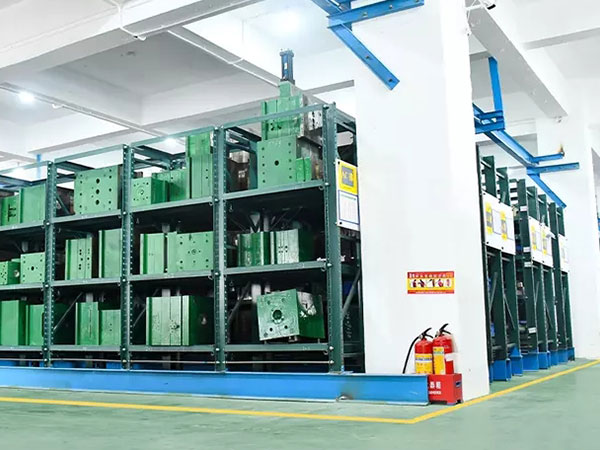
Accurate Delivery Time
NOBLE provides weekly progress reports to keep you informed of the progress.
- Our professional project management team of 50 project managers has completed more than 50,000 plastic injection mold projects with zero failure records.
- Each project is equipped with a project manager, and the project cycle is strictly controlled according to the plan. We provide a detailed mold schedule and weekly updates to keep you informed of the project status.
- NOBLE Provide online mold trial videos to let you know the mold operation, and send you samples for confirmation to ensure that they meet your requirements.
Types of Plastic Injection Molds
NOBLE offers all injection molds according to your requirements, from prototype molds to production and export molds, ensuring a reliable and high-quality service. Upload a CAD file to receive instant quotes, NOBLE will become your trusted injection mold manufacturer.
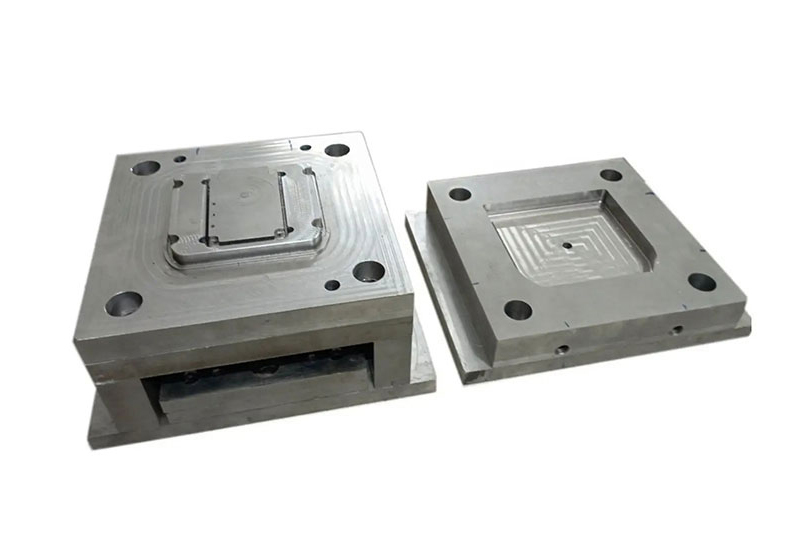
Single Cavity Mold
With premium single-cavity injection molds, you can produce plastic parts in low volumes effectively. These affordable choices for mold tooling allow you more control over the production of plastic.
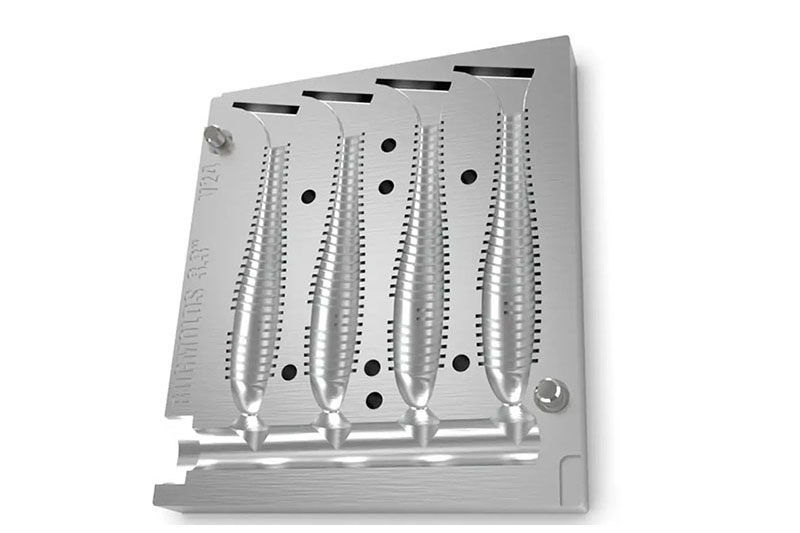
Stainless Steel
Using high-quality multi-cavity molds, produce numerous plastic molded parts quickly. Our multi-cavity injection molds guarantee more efficient cycle times while providing lower unit part costs. Higher productivity enables you to produce large numbers of parts per cycle.
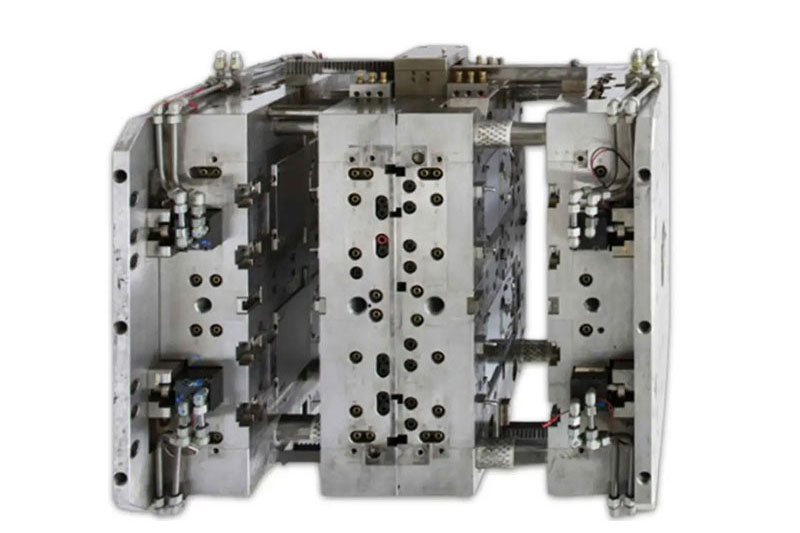
Stack Mold
Incorporating innovative laminated molds could enhance your injection molding process and reduce overall part costs. NOBLE increases your molding efficiency and throughput and even creates multi-component assemblies in a single pass. Choose from molds with the same or different numbers of cavities per parting face to best suit your needs.
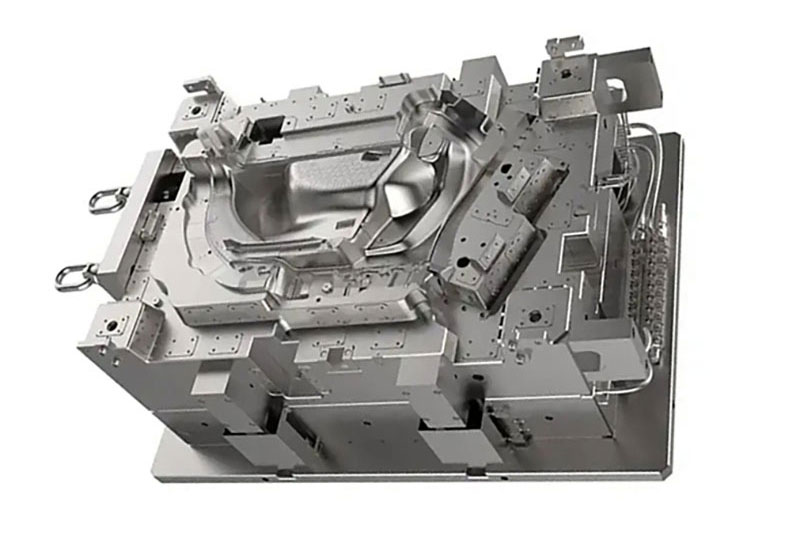
2K Injection Mold
A cost-effective approach for custom injection molding that uses two different plastic materials. For a product to seamlessly combine soft and hard plastics, we provide 2K injection mold tooling. Costs can be reduced by making products to order and integrating many assembly procedures into a single molding process.
Advantages of Injection Molding Tooling
Using molds in the production process can improve the stability of the material application, reduce losses, and ensure product quality. Numerous industries have benefited from the versatile use of molds. See below for the advantages of injection molds:
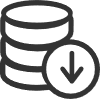
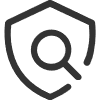
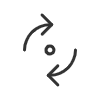
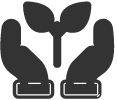
Our Injection Mold Tooling Processes
NOBLE specializes in creating custom molds tailored to your specific needs. Our team of expert engineers utilizes state of the art predictive modeling software to conduct thorough mold flow analysis, ensuring top-notch quality and efficient production.
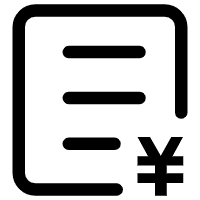
Request Instant Quote
From the moment we receive your inquiry email, our professional engineers will provide a response within 24 hours to ensure a smooth process.

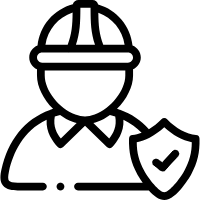
Engineer Evaluation
To ensure we can produce functional molds, we conduct a feasibility review of your design to ensure we can meet the requirements before commencing production.

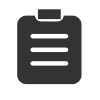
DFM Report
To ensure we can produce functional molds, we offer feasibility reviews of your design to ensure we can fulfill requirements before starting production.

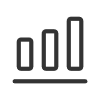
Mold Flow Analysis
Predictive modeling software helps us understand how the molten material moves and acts within the mold, which helps us make improvements.

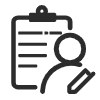
T1 Sample Inspection
Sampling will be delivered for you to review prior to manufacturing plastic parts to ensure precision and quality.

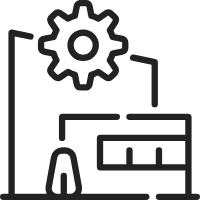
Low Volume Production
After the trial production phase, we begin batch production, which uses powerful machining to manufacture parts at fast rates to save on time and costs.

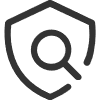
Strict Inspection
We follow international tolerance standards to ensure our parts meet your parameters.

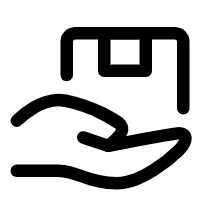
Delivery
As our team handles packaging to secure our parts neatly for transport, we partner with logistics companies to schedule a timely delivery to your region.
Injection Molding Tooling Tolerances and Standards
At NOBLE, we specialize in crafting custom injection molds with the utmost precision and top-notch materials. You can count on us for competitive pricing and timely delivery, regardless of whether you need tooling for small production runs or for larger-scale manufacturing. Our molds meet the highest international standards and are built to last, ensuring reliability and durability for all your projects.
Mold Class | Purpose | Shot Life | Tolerance | Lead Time |
Class 105 | Prototype Testing | Under 500 cycles | ± 0. 02mm | 7-10 days |
Class 104 | Low-volume Production | Under 100. 000 cycles | ± 0. 02mm | 10-15 days |
Class 103 | Low-volume Production | Under 500. 000 cycles | ± 0. 02mm | 10-15 days |
Class 102 | Medium-volume Production | Medium to high production | ± 0. 02mm | 10-15 days |
Class 101 | High-volume Production | Over 1, 000, 000 cycles | ± 0. 02mm | 10-18 days |
Materials for Custom Injection Mold Tooling
The choice of mold material largely determines its life and the quality of the injection molded part. NOBLE provides a diverse selection of material grades that cater to various stages of your product development. Our team also offers expert guidance on mold material selection to ensure optimal dimensional accuracy and aesthetic quality.
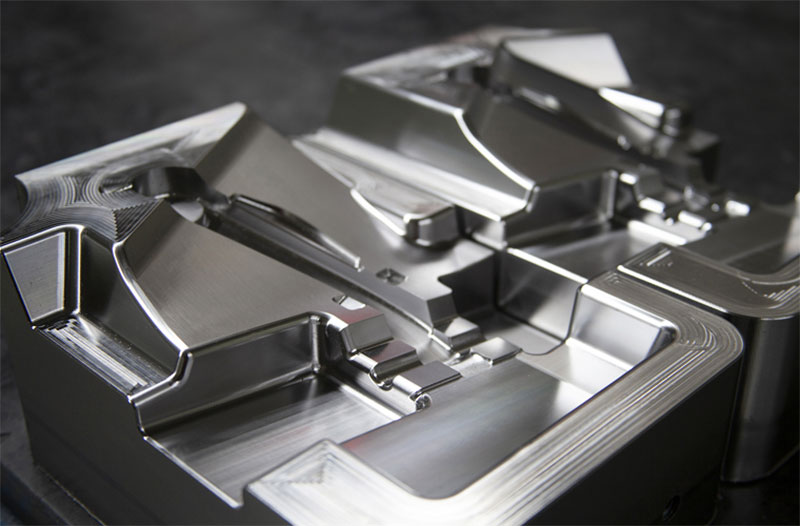
Tool Steel
Before starting the injection molding process in small or large batches, a CNC machined tool with high tolerances is necessary. Tool steel is the most commonly used material in such cases.
Types: P20, H13, S7, NAK80, S136, S136H, 718, 718H, 738
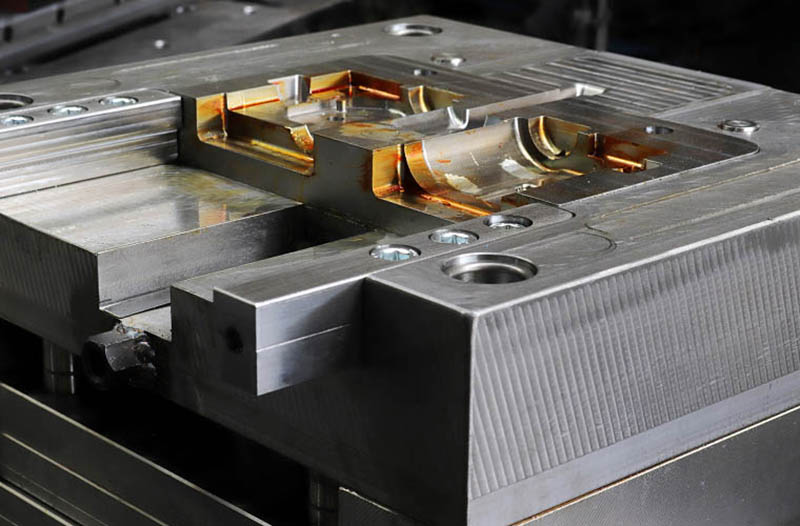
Stainless Steel
Steel and stainless steel are the primary materials used to create injection molds, but their manufacturing costs are quite high. As a result, these molds are generally reserved for large-scale productions.
4Types: 420, NAK80, S136, 316L, 316, 301, 303, 304
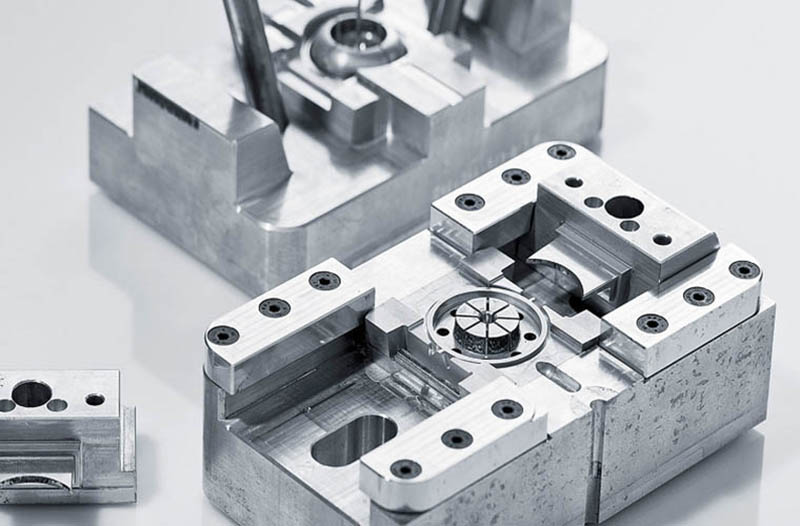
Aluminum
Aluminum molds are a cost-effective alternative to traditional steel and carbon steel injection molds. They not only cost less but also provide faster cycles and quicker turnaround times, which is especially useful for testing markets.
Types: 6061, 5052, 7075
Surface Finishes for Injection Mold Tooling
Our superior surface finishes can make your custom injection molds stand out even more. We offer a diverse range of finishing solutions to enhance the surface quality of your molds. These coatings also improve the mechanical strength and durability of your molds.
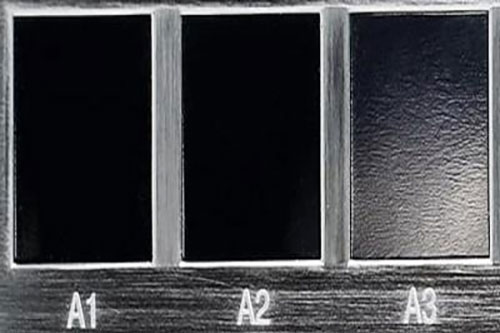
Glossy
A grade finishes are made using a diamond buffing process and yield shiny and glossy surfaces on injection molded parts.
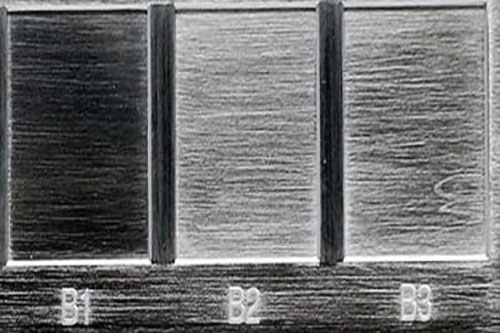
Semi-glossy
B grade finishes use grit sandpaper to produce parts with a slightly rougher finish than grade A parts. Custom molded plastic parts that undergo B grade finishing have a matte surface texture.
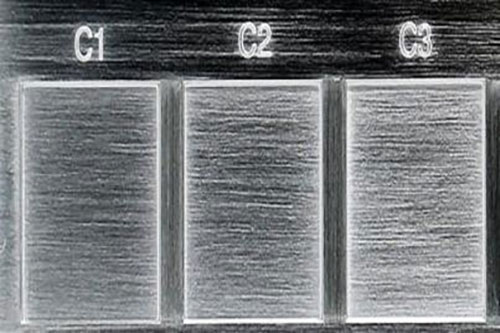
Matte
C grade finishes use grit sanding stones to produce a rough, uneven surface. Injection plastic parts that undergo C grade finishing have a matte surface texture.
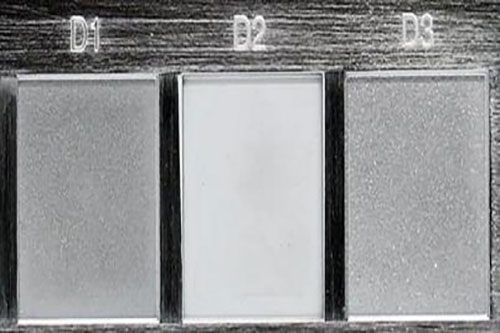
Textured
D grade finishes use grit and dry glass beads or oxide to produce a very rough textured finish. Depending on the type of material used, products can have a satin or dull finish.
Strict Quality Control for Injection Molds
NOBLE has an experienced team of engineers. Through the fine design of injection molds and strict quality control of the process, we ensure that our strict quality standards are met. In the end, you will get a high-precision mold with low cost, stable performance, and long life.
- Material Certificate
- Free DFM Design Feedback
- Weekly Mold Progress Report
- Trial Mold Parameter & Video Supplying
- T1 samples Inspection Report
- Inspection Report Before Shipment
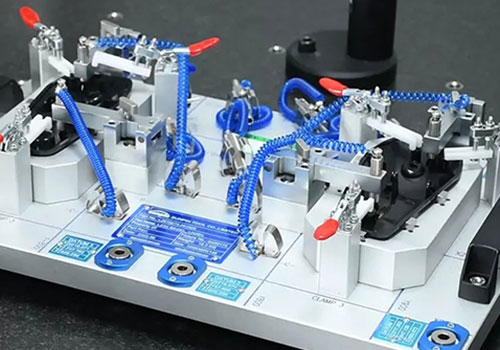
Custom Injection Molding Tooling Display
NOBLE has more than 10 years of experience in injection molding Tooling. It is equipped with advanced injection mold production equipment and experienced engineers to manufacture unparalleled high-precision stacked molds, multi-cavity molds, 2k injection molds, high-precision molds, etc. with high life expectancy at competitive prices.
See What Our Customers Say About Us
Customer feedback carries more weight than company claims – check out what our valued customers have to say about our injection mold services.
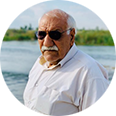
Piscary Herskovic
Product Designer
NOBLE has been our quality supplier of injection mold tooling. Fast delivery is essential for our business, and NOBLE always offers short lead time and competitive pricing. Andy responds quickly to all our emails and questions. This has improved our working relationship, and we continue to value this partnership.
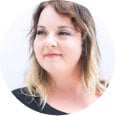
Hari Mackenzie
Engineer
We asked NOBLE to fabricate parts for an acritical supplier demo, and you came through with a short lead time. Your work is alwayshigh quality, and we are grateful for your precision in injection mold tooling. The help in checking our designs and material selection has also saved our company from making expensive errors.
We look forward to doing future projects with you guys.
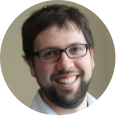
Mark Alford
Vice President
From the instant and accurate quotation to the production process to the timely delivery of parts, NOBLE responded to our demands with complete professionalism. They handled every aspect of this injection mold tooling project quickly and cost-effectively. We will surely work with them again in the future.
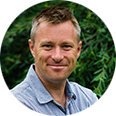
Kris Olarte
Vice President
I’ve worked with the NOBLE team in the past, they always do a perfect job. The responsiveness and ability to quote within a day make them my first choice to work with. They also are very good communicators and understand my design needs on a deep level or ask pertinent questions to ensure they do a perfect job.
What is Injection Molding Tooling?
Injection mold tooling refers to the process of designing and manufacturing the molds used in the injection molding process. Injection molding is a popular manufacturing technique for producing various plastic products, from small components to large, complex parts. The injection mold tooling process is crucial for the success and efficiency of the injection molding process.
The injection mold is made up of two halves, called the core and the cavity, which fit together precisely. When the mold is closed, the cavity creates a hollow space in the shape of the desired product. Molten plastic is then injected into this space, where it cools and solidifies to form the final product.
Injection Molding Tooling Applications
Because CNC machining can achieve high precision without changing the material structure with good manufacturing speed, it is becoming growing common as the range of machines, control systems, and tools for CNC machining continues to expand.NOBLE is dedicated to providing precision machining services for various industries and our precision CNC-crafted parts can be found in all areas of the industry, including.

Oil & Gas
Experts at NOBLE master the comprehensive knowledge of CNC machining for the oil field and gas industry paired with the assurance of high precision offered by top-notch CNC machines.
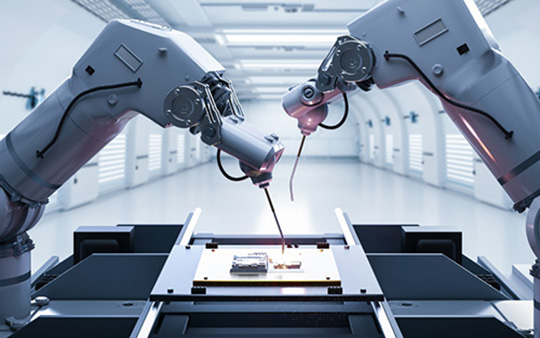
Automation Equipment
NOBLE Rapid Prototyping service allows you to quickly and easily create automated functional prototypes to test and optimize your design, select the right process, reduce costs, and shorten project cycles. On-demand services can produce automated parts with a high level of accuracy.
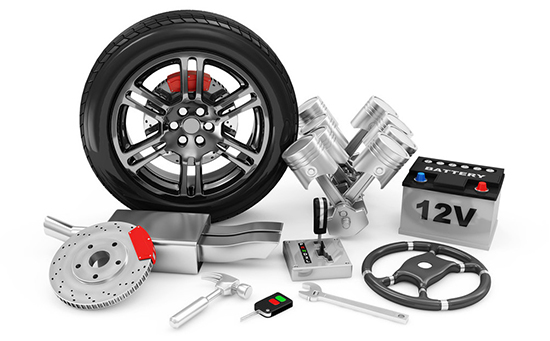
Automotive
Our low-volume manufacturing services is the ideal manufacturing solution for on demand automotive parts.
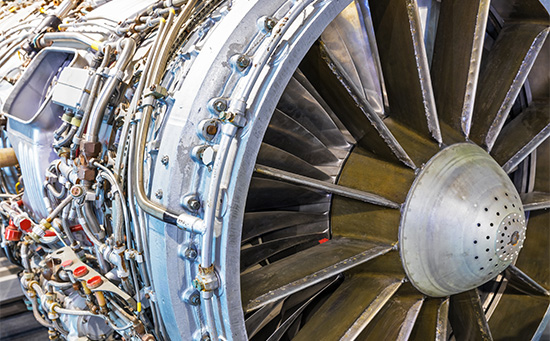
Aerospace
The durability and precision that our precison manufacturing services provide meets the sophisticated needs the different phases of the aerospace industry required.
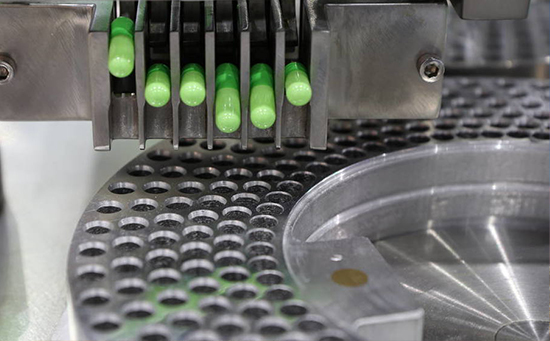
Medical Devices
Medical supplies manufacturers, tech startups, and research labs benefit significantly from the prototyping solutions we provide.
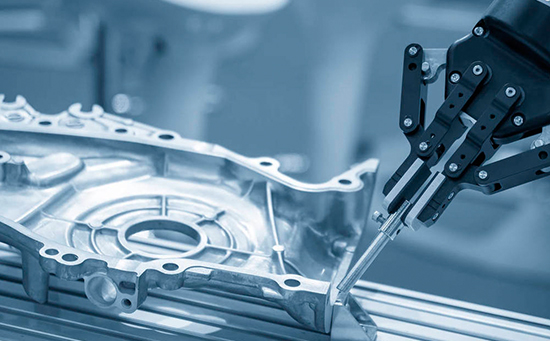
Robotics
Our industrial-grade robotics prototyping and parts manufacturing services aid in the continuous evolution of the robotics market.
If you are looking for a rapid prototyping manufacturer or a CNC machine shop to fabricate small, medium-volume, or mass-production products, NOBLE is an ideal choice.Our well-trained and experienced staff manufactures parts in line with drawings on modern CNC machines, with the highest accuracy and processing quality in all sizes.In addition, we provide professional design considerations for your CNC machining projects.
Want to get the most professional and fastest service for your CNC machining project? Upload your CAD files now and obtain a quote!
Injection Mold Tooling of FAQs
Steel, aluminum, or beryllium-copper alloy are frequently used to make hardened or pre-hardened plastic injection molds. Steel molds are more expensive yet are frequently chosen due to their excellent durability.
The cost is depended on your requirements, many factors contribute to the price, like the size of the component, mold complexity, number of injection cavities, materials, post-processing needs, etc.
The first step in mold design is choosing the mold’s material, form, size, capacity, and other details. Also, during this step, factors like the manufacturing temperature requirements, the materials utilized, and the required qualities of the finished product must be taken into account.
The mechanics that enable a mold to produce a high-quality final product are made up of mold components. Mold bases, pins, ejectors, lifters, bushings, guides, and alignment tools are important parts. Frame plates, frame components, and cavity tooling are the three subcategories of mold components.
The lifespan of injection molding tooling can vary depending on several factors, such as the material being molded, the design of the tooling, the complexity of the part being produced, and the quality of maintenance and care given to the tooling. In general, injection molding tooling can last for thousands to hundreds of thousands of cycles before it needs to be replaced or refurbished. However, this can vary widely depending on the specific circumstances of each production run.