Die Casting Services
Our Custom Die Casting Services
With competitive prices and unmatched precision, from aluminum alloy prototyping to die-cast production, get impeccable and stable performance aluminum alloy die-cast parts, and get free die-casting quotes and design feedback within hours.
- Advanced Equipment & Cost-Effective Price
- ISO 9001 & ISO13485 Certified Factory
- 10+ Years of Die Casting
- Tolerance down to 0.001mm
- Instant Die Casting Quotes
- 7/24 Technical Support
STEP | STP | STL | IGS | IGES | PRT | SLDPRT | SAT | X_T | IPT | CATPART | PDF
Max. file size: ≤20MB
- All uploads are secure and confidential.
Our Precision Die Casting Services
NOBLE has been offering die casting services to various industries for over 10 years. We provide a range of manufacturing options to choose from, and our skilled team can help with design optimization, material selection, and manufacturability evaluation. Help provide robust and durable parts and prototypes.
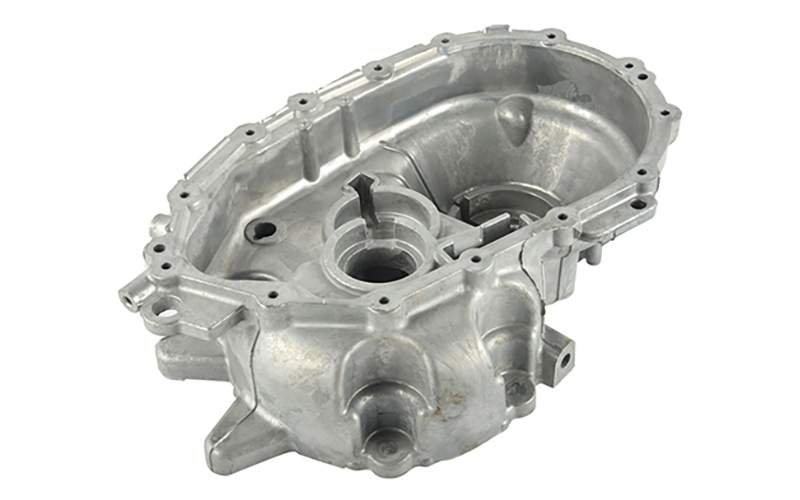
Hot chamber die casting, also known as gooseneck casting, is a manufacturing process that is mainly used for casting metals with low melting points like zinc, tin, and lead-based alloys. One notable aspect of this process is that the metal is melted and kept in a furnace that is connected to the die casting machine. Benefits of hot chamber die casting includes faster cycle times, reduced energy consumption, and lower equipment expenses. However, it is limited to low-melting materials due to the fact that the molten metal comes into direct contact with the furnace and other components.
- 100% Part Inspection
- Versatility and Precision
- No minimum order quantity
- Competitive & Affordable Price
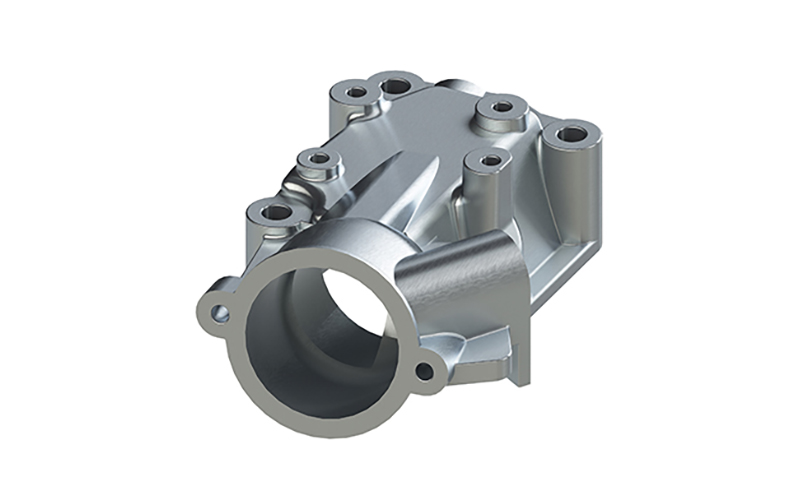
Cold chamber die casting also called injection die casting, is a method used for casting metals with high melting points, like copper, aluminum, and magnesium alloys. This process involves introducing the molten metal into a mold cavity from an external furnace instead of keeping it in the machine. Cold chamber die casting offers several advantages, including the ability to cast high melting point alloys, better control of molten metal temperature, and reduced wear on machine components. However, it typically has longer cycle times compared to hot chamber die casting.
- High Casting Quality
- Direct Delivery to You
- High Production Efficiency
- Wide Range of Raw Materials
Our Custom Die Casting Molds Services
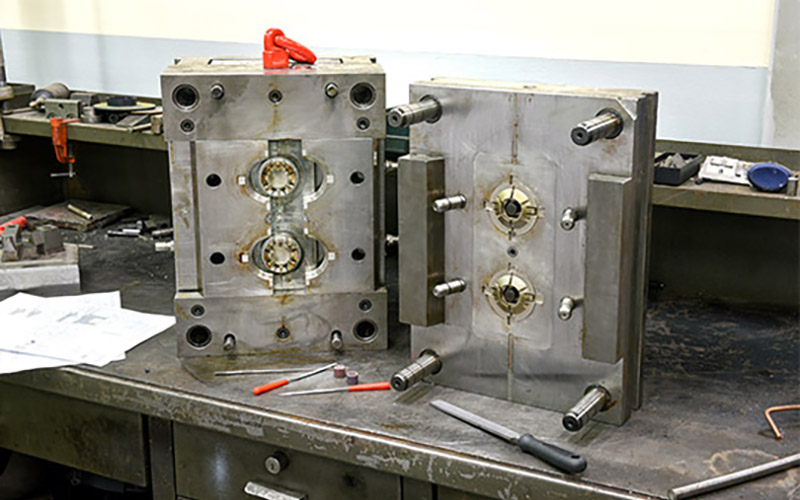
Create reliable small precision die-casting molds for custom die-cast parts. Let you get accurate and excellent custom die-casting molds to produce high-quality die-casting parts. Leverage our commitment to quality, fast production, and competitive pricing to produce long-life, high stability die casting molds.
- Large Scale Production
- Lower Production Cost
- High Precision & Efficiency
- Competitive & Affordable Price
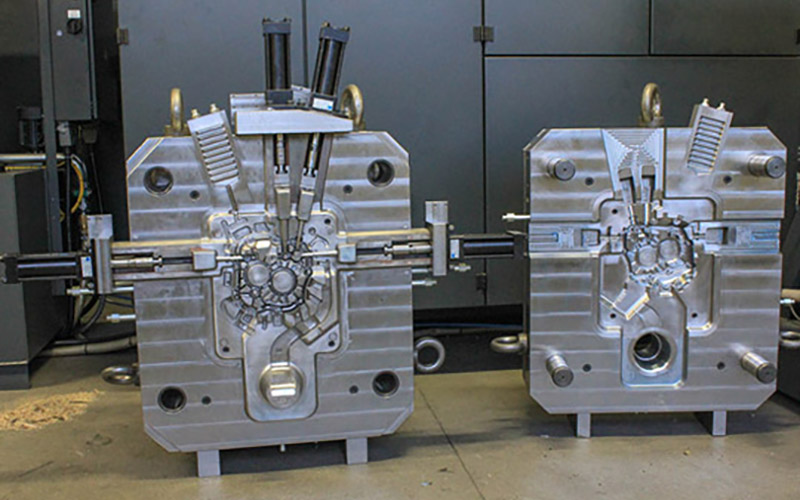
With more than 10 years of rich die-casting mold experience, advanced die-casting mold equipment, and professional technical engineers, NOBLE produces long-life, high-stability, and consistent die-casting molds at competitive prices. NOBLE is good at designing and manufacturing die-casting molds for auto parts, 5G communication equipment, aviation parts, electrical and electronic, and medical equipment.
- Fast Cycle Time
- Superior Thermal Conductivity
- Competitive & Affordable Price
- High Precision and Dimensional Stability
Our Robust Die Casting Capabilities
From Prototyping to Manufacturing
NOBLE is your trusted one-stop custom manufacturing solution, from prototype design to manufacturing, through huge manufacturing resources, suitable technology, streamlined process, expert guidance, and perfect quality inspection process to turn your ideas into reality.
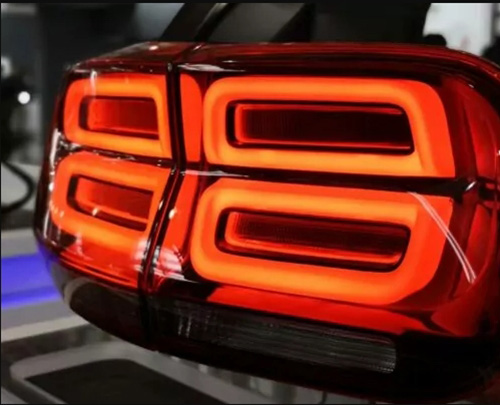
Prototype Machining
From NOBLE, get an online quote with free design analysis in hours to get your CNC machined prototypes done in days.
- State-of-the-art Equipment
- 10+ Years of CNC Machining
- Competitive & Affordable Price
- Quote Within 24 hours
- Free DFM Feedback
- Fast Turnaround in 7 days
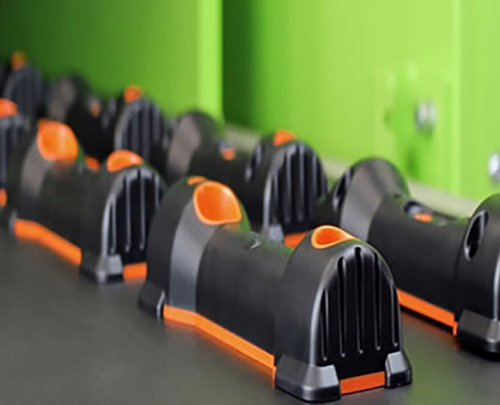
Low-Volume Manufacturing
With advanced production equipment and an experienced team of engineers, we can manufacture products with complex geometric shapes and high precision requirements with strict tolerance control and perfect quality inspection processes.
- Competitive & Affordable Price
- State-of-the-art Equipment
- 10+ Years of Low-Volume Manufacturing
- Fast Lead Time
- 30+ Countries shipped
- 100% Part Inspection
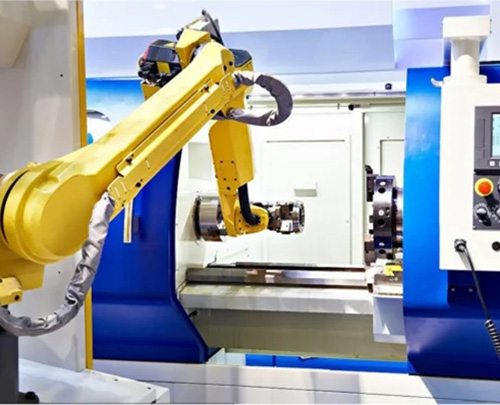
Medium & Mass Production
NOBLE meets mass production needs through strict tolerance control, quality inspection, and a complete supply chain, and quickly delivers cost-effective, high-precision parts.
- 10+ Years of Medium&Mass Production
- Competitive & Affordable Price
- Large Supplier Network
- 100,0000+ Unique parts produced
- Guaranteed Consistent Quality
- Fast Turn-Around Production
Why Choose Us for Custom Die Casting Services
NOBLE uses advanced technology and has a team of skilled professionals who are dedicated to putting our customers first. Our die casting services are precise, efficient, cost-effective, and produce high-quality results. By choosing our die casting services, you can elevate your business to new levels of success.
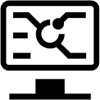
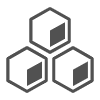
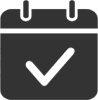
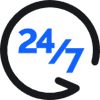
Work with Us in 4 Simple Steps Only
With many years of manufacturing experience, NOBLE offers the best solutions for all rapid prototyping and low-volume manufacturing needs. We streamline the innovation cycle into four simple but effective steps.



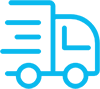
Die Casting Tolerances and Standards
With precision die casting services, NOBLE is your ideal partner to create precision machined prototypes and parts tolereance is down to 0.001. We can also achieve special tolerances as long as you indicate your requirements for your drawing.
Dimension | Standards |
Minimum part weight | 0.017 kg |
Maximum part weight | 12 kg |
Minimum part size | ∅17 mm × 4 mm |
Maximum part size | 300 mm × 650 mm |
Minimum wall thickness | 0.8 mm |
Maximum wall thickness | 12.7 mm |
Tolerance class for casting | ISO 8062 ST5 |
Minimum possible batch | 1000 pcs |
Materials for Custom Die Casting Parts
Metals with low fusing temperatures, such as aluminum, zinc, magnesium, lead, and copper, are commonly used in die casting. Some ferrous and uncommon metals, however, can also be used. Some common materials as following:
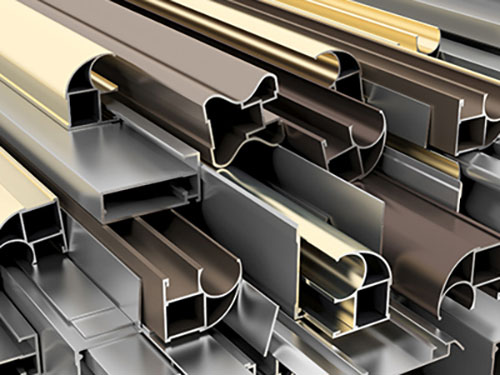
Aluminum
Aluminum die casting offers numerous advantages, including lightweight construction, high strength-to-weight ratio, excellent machinability, thermal conductivity, corrosion resistance, design flexibility, cost efficiency, and recyclability. These properties make aluminum a popular choice for various applications and contribute to its widespread use in die casting processes.
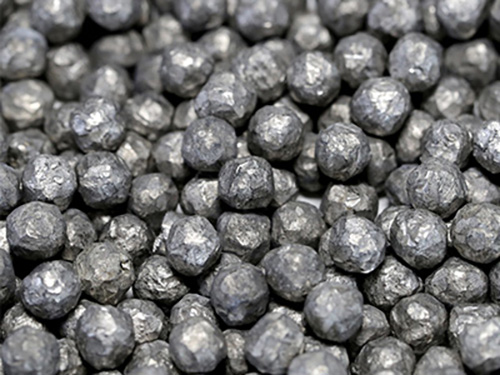
Magnesium
Magnesium’s lightweight nature, high strength-to-weight ratio, excellent machinability, heat dissipation properties, dimensional stability, EMI/RF shielding capabilities, and recyclability make it a valuable material for die casting. Its unique combination of properties opens up opportunities for lightweight and high-performance components in industries such as automotive, aerospace, electronics, and consumer goods.
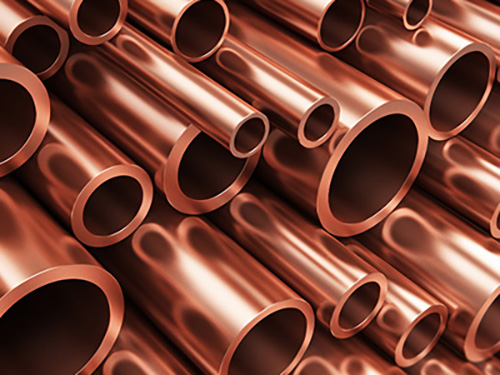
Copper
Traditional die casting processes usually avoid using copper due to its high melting point and challenging properties. However, a specific variant called copper alloy die casting is designed for casting copper-based alloys. This specialized technique produces high-quality copper-based components that offer excellent corrosion resistance and strength. Despite not being commonly used, copper alloy die casting is tailored to the unique properties and requirements of copper-based alloys, making them suitable for a range of industries and applications.
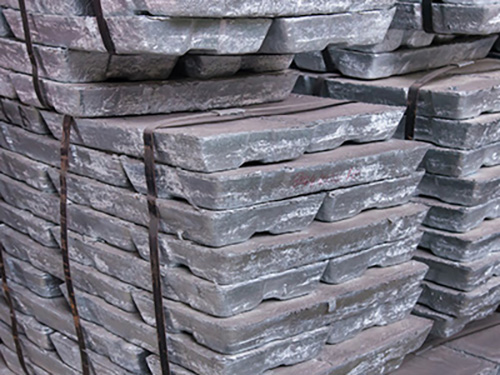
Zinc
Zinc die casting offers several advantages, including excellent castability, high strength, corrosion resistance, design flexibility, high production efficiency, and recyclability. These properties make zinc a popular choice for a wide range of applications, particularly those that require complex shapes, precision, and cost-effective production. including automotive, electronics, telecommunications, consumer goods, and more. Common examples of zinc die cast components include automotive parts, electrical connectors, door handles, hinges, faucets, and various household appliances.
Surface Finishes for Die Casting
NOBLE can help improve the surface qualities of your products by offering a diverse range of surface finishes. Surface finishes on your customized parts aim to improve their appearance, surface hardness, and roughness, chemical and corrosion resistance, and so on. They also aid in the concealment of any visible tool marks from areas cut with live tooling. Here are some of your best options.
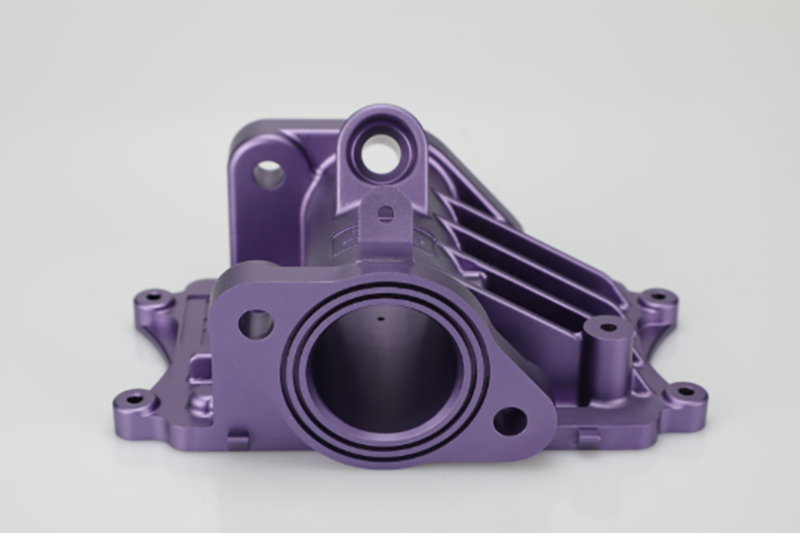
Anodizing
Anodizing improves corrosion resistance, enhancing wear resistance and hardness, and protecting the metal surface. Widely used in mechanical parts, aircraft, and automobile parts, precision instruments, etc.
Materials: Aluminum
Color: Clear, black, grey, red, blue, gold.
Texture: Smooth, matte finish
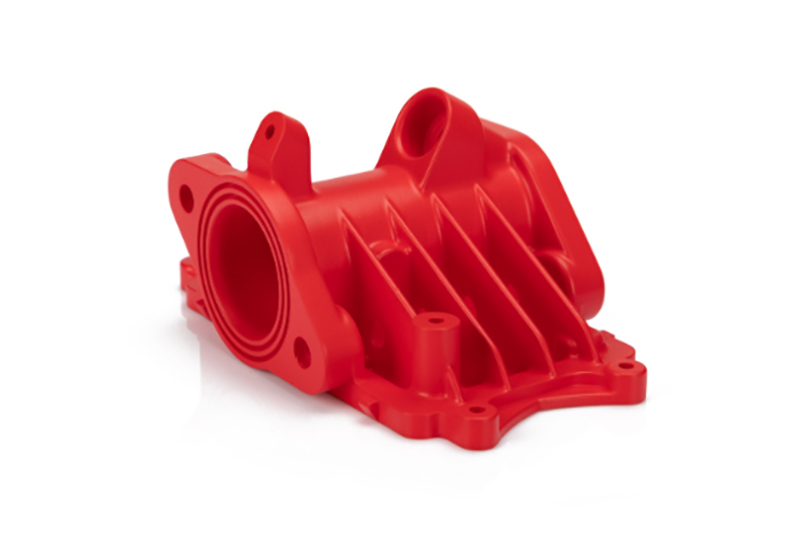
Powder Coating
Powder coating is a type of coating that is applied as a free-flowing, dry powder. Unlike conventional liquid paint which is delivered via an evaporating solvent, powder coating is typically applied electrostatically and then cured under heat or with ultraviolet light.
Materials: Aluminum, Stainless Steel, Steel
Color: Black, any RAL code or Pantone number
Texture: Gloss or semi-gloss
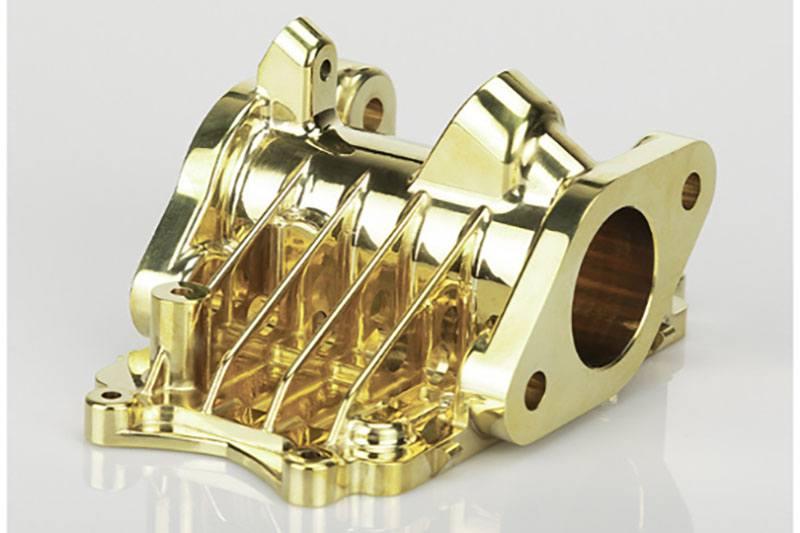
Electroplating
Electroplating can be functional, decorative or corrosion-related. Many industries use the process, including the automotive sector, in which chrome-plating of steel automobile parts is common.
Materials: Aluminum, steel, Stainless Steel
Color: N/A
Texture: Smooth, Glossy finish
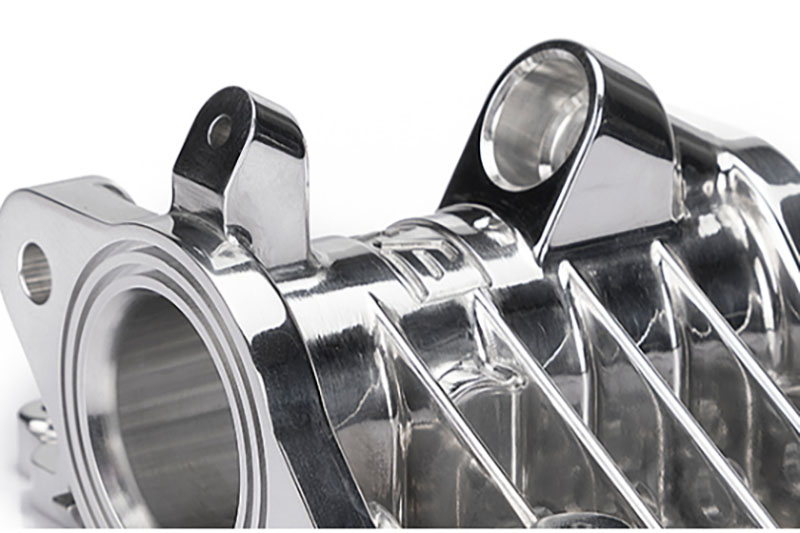
Polishing
Polishing is the process of creating a smooth and shiny surface, either through physical rubbing of the part or by chemical interference. The process produces a surface with significant specular reflection, but in some materials is able to reduce diffuse reflection.
Materials: Aluminum, Brass, Stainless Steel, Steel
Color: N/A
Texture: Glossy
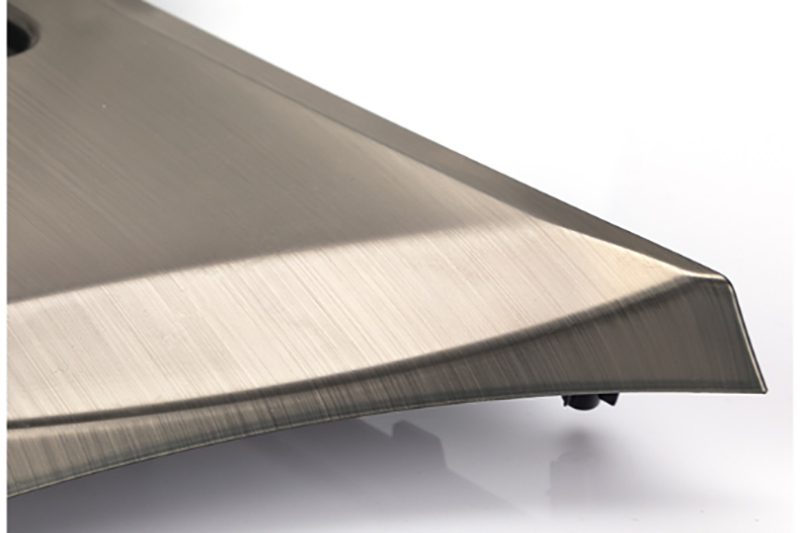
Brushing
Brushing is a surface treatment process in which abrasive belts are used to draw traces on the surface of a material, usually for aesthetic purposes.
Materials: ABS, Aluminum, Brass, Stainless Steel, Steel
Color: N/A
Texture: Satin
Custom Die Casting Parts Display
Please take a look at our customized precision aluminum alloy die-casting parts for valued customers, from prototype design to die-casting molding, to obtain impeccable surface treatment and stable performance of aluminum alloy die-casting parts at competitive prices.
See What Our Customers Say About Us
NOBLE has been engaged in die casting services for over ten years and has served many overseas customers. Customers’ words are more substantively representative than the company’s statement–see the objective evaluation of our satisfied customers.
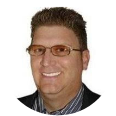
Lucas
Automative Engineer
I have been working with this NOBLE for my diecasting needs for several years now, and their commitment to excellence never ceases to amaze me. Their die casting expertise is unparalleled, and they consistently deliver exceptional results. What truly sets them apart is their outstanding customer support. They are responsive, and proactive, and provide regular updates throughout the manufacturing process. I have complete confidence in their abilities and highly recommend their die casting services to anyone seeking top-quality manufacturing solutions.
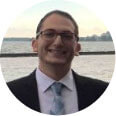
Benjamin
Vice President
I am extremely satisfied with the results of NOBLE’s die-casting services. Not only did they produce high-quality die-cast parts, but they also ensured prompt delivery within the agreed timeline. The attention to detail exhibited by their team was commendable, resulting in parts that met my exact specifications. The company’s commitment to quality and precision is evident in every aspect of its work. I appreciate their professionalism, reliability, and dedication to customer satisfaction. If you’re searching for reliable die casting services with on-time delivery, I truly recommend them.
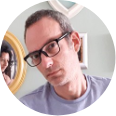
Ethan
Senior Engineer
I had the pleasure of working with NOBLE for my complex die casting project, and I am delighted with the outcome. Their die casting services exceeded my expectations in every way. The team’s technical expertise, coupled with their state-of-the-art equipment, ensured the production of flawless die-cast parts. The attention to detail, precision, and commitment to quality were evident throughout the entire process. Additionally, their excellent project management and clear communication made the entire experience seamless and hassle-free. I highly recommend their die casting services to anyone seeking top-tier manufacturing solutions that deliver exceptional results.
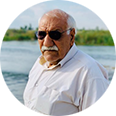
Alexander
Lead Engineer
I recently had the pleasure of utilizing the die casting services provided by NOBLE, and I must say, I am thoroughly impressed. From start to finish, their professionalism and attention to detail were exceptional. The team worked closely with me to understand my project requirements and delivered outstanding results. The die-cast parts produced were of impeccable quality, with precise dimensions and flawless finishes. The customer service was top-notch, and the turnaround time was impressive. I highly recommend their die casting services to anyone in need of high-quality, reliable, and efficient manufacturing solutions.
Die Casting Applications
Die casting plays an important role in parts manufacturing in automotive, aerospace, electronics, appliances, telecommunications, and medical equipment. NOBLE specializes in providing cutting-edge manufacturing solutions for various industrial applications. Our focus is on delivering superior quality parts at competitive prices to valued customers across multiple industries.

Oil & Gas
Die casting plays a vital role in making it an ideal manufacturing process for components used in solar power generation, wind energy, electric vehicles, energy storage, hydrogen fuel cells, and energy-efficient solutions. As the demand for sustainable energy technologies continues to grow, die casting will remain a key enabler in the production of critical components for new energy applications.
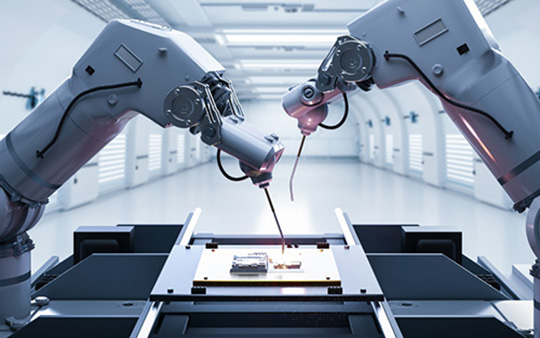
Automation Equipment
NOBLE Rapid Prototyping service allows you to quickly and easily create automated functional prototypes to test and optimize your design, select the right process, reduce costs, and shorten project cycles. On-demand services can produce automated parts with a high level of accuracy.
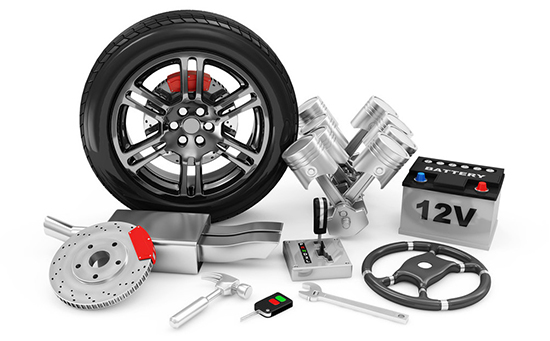
Automotive
Die casting's ability to produce complex shapes, maintain tight tolerances, and deliver high-quality finished parts makes it an ideal manufacturing process for numerous automotive components. The efficiency, cost-effectiveness, and versatility of die casting contribute to the continuous advancement and innovation in the automotive industry. Common parts include gears, cylinders, gladhands, transfer cases, small engine parts.
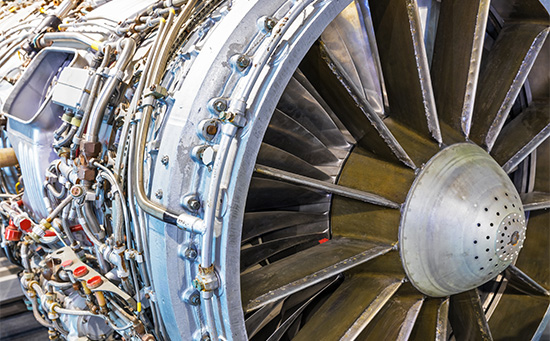
Aerospace
Die casting's ability to produce complex shapes, maintain tight tolerances, and deliver high-quality finished parts makes it an ideal manufacturing process for numerous automotive components. The efficiency, cost-effectiveness, and versatility of die casting contribute to the continuous advancement and innovation in the automotive industry. Common parts include gears, cylinders, gladhands, transfer cases, small engine parts.
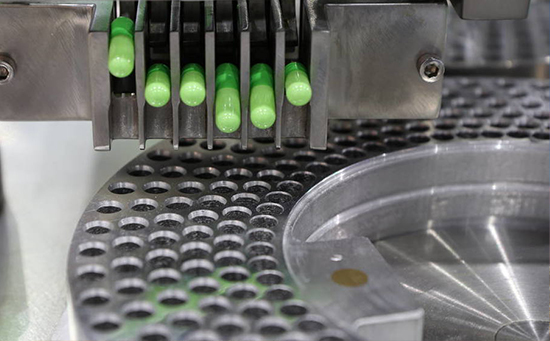
Medical Devices
The precise and durable characteristics of die-cast components contribute to the safety, functionality, and effectiveness of medical devices and equipment. Common parts like forceps, clamps, retractors, and scalpel handles, prosthetic limbs, joint implants, and fixation devices.
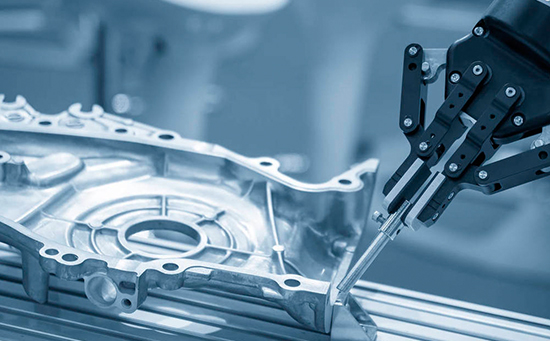
Robotics
Die casting offers numerous advantages in the robotic industry, including the ability to produce complex geometries, high precision, cost efficiency, and integration of functional features. These advantages contribute to the development of robust, efficient, and high-performing robotic systems capable of meeting the demanding requirements of automation and industrial applications. Common parts include robot frames and housings, motor housings, joints and linkages, etc.
If you are looking for a rapid prototyping manufacturer or a CNC machine shop to fabricate small, medium-volume, or mass-production products, NOBLE is an ideal choice.Our well-trained and experienced staff manufactures parts in line with drawings on modern CNC machines, with the highest accuracy and processing quality in all sizes.In addition, we provide professional design considerations for your CNC machining projects.
Want to get the most professional and fastest service for your CNC machining project? Upload your CAD files now and obtain a quote!
Die Casting FAQs
Die casting involves injecting molten metal into a mold cavity at high pressure. The metal then solidifies and takes on the precise shape of the mold, creating a finished part that is complex and accurate. This process is often used to produce top-quality metal components with exceptional surface finish and dimensional accuracy.
Die casting can be performed using a variety of materials, including aluminum, zinc, magnesium, and copper-based alloys. Aluminum is the most commonly used material in die casting due to its lightweight, high strength-to-weight ratio, and excellent thermal conductivity. Zinc alloys are often chosen for their superior casting properties and cost-effectiveness. Magnesium and copper-based alloys are preferred for applications that require specific mechanical or thermal properties.
Die casting offers several advantages over other manufacturing processes. These include:
High dimensional accuracy and repeatability
Excellent surface finish and intricate detailing
Fast production cycle times
Ability to produce complex shapes with thin walls
Good mechanical properties and strength
Cost-effective for high-volume production
Minimal post-processing required
Die casting finds application in a wide range of industries, including automotive, aerospace, electronics, appliances, telecommunications, and medical equipment. It is used to manufacture components such as engine parts, transmission housings, chassis components, electronic enclosures, heat sinks, and various consumer products. Die casting is favored in industries that require high-volume production of complex, lightweight, and dimensionally accurate parts.
Die casting is a casting process that uses a metal mold, called a die, to produce intricate and accurately shaped metal parts, while casting refers to a broader category of processes that involve pouring molten material into a mold to create a desired shape.
Forging involves shaping metal by applying compressive forces, typically using a hammer or press, while die casting is a process of creating metal parts by injecting molten metal into a die under high pressure.
Die casting offers greater precision, faster production cycles, and the ability to create complex shapes with tight tolerances compared to sand casting, making it a preferred choice for high-volume production of intricate metal parts.
Sand die casting, also known as sand casting or sand-molded casting, is a casting process that uses sand as the mold material to create complex metal parts. In this process, a pattern is pressed into a sand mold, molten metal is poured into the mold cavity, and once solidified, the sand mold is broken apart to retrieve the cast metal part.
There are two main types of die-casting processes:
Hot Chamber Die Casting:In this method, the molten metal is held in a furnace connected to the die-casting machine. A gooseneck ladle or a piston injects the molten metal into the die under high pressure. Hot chamber die casting is commonly used for materials with low melting points, such as zinc, tin, and lead alloys.
Cold Chamber Die Casting:In this process, the molten metal is ladled into a separate cold chamber before being injected into the die. The metal is pushed into the die cavity using a plunger or hydraulic pressure. Cold chamber die casting is suitable for materials with high melting points, such as aluminum, copper, and magnesium alloys.
In general, die casting is more expensive than sand casting. The initial setup costs for die casting, including the design and production of the mold, are higher compared to sand casting, where molds can be made from readily available materials like sand. However, die casting offers advantages such as faster production cycles, higher dimensional accuracy, and the ability to produce complex shapes, which can offset the higher initial costs for certain applications. Sand casting is typically more cost-effective for lower volume production or when the design requirements allow for looser tolerances.
Aluminum is commonly used for die casting due to several advantageous properties it possesses:
Lightweight:Aluminum has a low density, making it ideal for applications where weight reduction is important, such as in the automotive and aerospace industries.
Excellent Machinability:Aluminum alloys used in die casting have good machinability, allowing for easy shaping, drilling, and finishing operations.
High Thermal Conductivity:Aluminum has excellent thermal conductivity, which enables efficient heat dissipation and makes it suitable for applications involving heat transfer.
Corrosion Resistance: Aluminum alloys exhibit good resistance to corrosion, making them suitable for use in various environments.
High Strength-to-Weight Ratio:Aluminum alloys used in die casting offer a favorable strength-to-weight ratio, providing structural integrity and reducing overall weight.
Recyclability:Aluminum is highly recyclable, allowing for environmentally friendly production and reducing the need for primary raw materials.
The main difference between extruding and casting of aluminum lies in the manufacturing processes:
Aluminum Extrusion:Extrusion is a process where a billet or a heated cylindrical piece of aluminum is forced through a shaped die under high pressure to form a continuous profile with a consistent cross-section. This process is used to produce long, uniform shapes such as rods, tubes, and profiles with complex cross-sectional designs.
Aluminum Casting:Casting involves pouring molten aluminum into a mold or cavity and allowing it to solidify to obtain the desired shape. There are various casting methods, including sand casting, die casting, and investment casting. Casting is commonly used to create intricate and detailed parts that may not be easily achievable through extrusion.
The most widely used materials for die casting are aluminum alloys, particularly those from the aluminum-magnesium (Al-Mg) and aluminum-silicon (Al-Si) families. These alloys offer a good combination of properties such as high strength, low density, good casting fluidity, and excellent corrosion resistance. Aluminum die casting is extensively used in various industries, including automotive, aerospace, electronics, consumer goods, and more. Other materials such as zinc, magnesium, and copper alloys are also used in die casting, but aluminum alloys dominate the die casting industry in terms of usage.
Automotive:Aluminum die casting is extensively used in the automotive industry for parts such as engine blocks, cylinder heads, transmission cases, suspension components, and various structural components. The lightweight nature, excellent strength-to-weight ratio, and good thermal conductivity of aluminum make it highly suitable for improving fuel efficiency and reducing vehicle weight.
Aerospace:The aerospace industry utilizes aluminum die casting for components like aircraft engine parts, structural components, and interior parts. The combination of lightweight properties, high strength, and corrosion resistance makes aluminum alloys a preferred choice for aerospace applications.
Electronics:Aluminum die casting is employed in the electronics industry for heat sinks, enclosures, and housings for electronic devices. The excellent thermal conductivity of aluminum aids in heat dissipation, ensuring the efficient operation and longevity of electronic components.
Consumer Goods:Various consumer products, such as power tools, home appliances, sporting goods, and furniture, utilize aluminum die casting for their components. The lightweight, durable, and aesthetically appealing properties of aluminum make it suitable for a wide range of consumer goods.
Telecommunications:Telecommunication equipment manufacturers often use aluminum die casting for enclosures, frames, and structural components of devices like routers, switches, and communication towers. The combination of lightweight construction and good electromagnetic shielding properties makes aluminum alloys well-suited for telecommunications applications.
Die cast aluminum typically has a tensile strength ranging from 170 MPa (25,000 psi) to 450 MPa (65,000 psi), depending on the specific alloy and heat treatment, making it suitable for a wide range of applications.