Die Casting Mold Service
Our Custom Die Casting Mold Making Services
Providing high-precision and long-life die-casting mold services at competitive prices, combining cutting-edge die-casting mold technology with advanced production equipment, our expert engineers are dedicated to reducing cycle times by up to 50%+, with fast turnaround, obtaining in minutes Get a quote and getting your die casting mold within days.
- ISO 9001 & ISO13485 Certified Factory
- 10+ Years of Die Casting Mold Making
- Advanced Equipment & Competitive Price
- Get an Instant Die Casting Mold Making Quote
- Professional & Free DFM Report
- 24/7 Engineering Support
- Lead Time As Fast As 3 Days
STEP | STP | STL | IGS | IGES | PRT | SLDPRT | SAT | X_T | IPT | CATPART | PDF
Max. file size: ≤20MB
- All uploads are secure and confidential.
Our Powerful Die Casting Molds Processes
There are several types of die-casting toolings, and they have different functions depending on the requirements. They include:
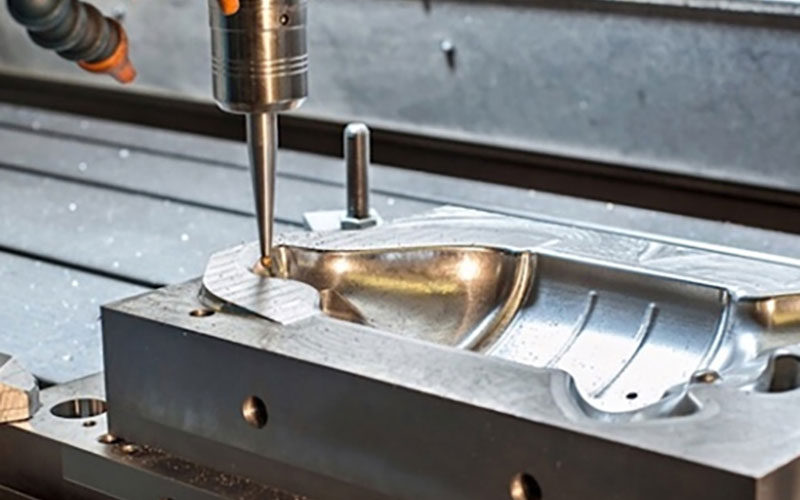
Prototypes are typically made using these dies. The tooling procedure and its features are identical to those of production dies. To cut tooling costs, complicated features are, nevertheless, simplified and machined with less accuracy.
- High-Speed Production
- Fast Turnaround in 7 days
- High Electrical Conductivity
- Free Dimensional Inspection Reports
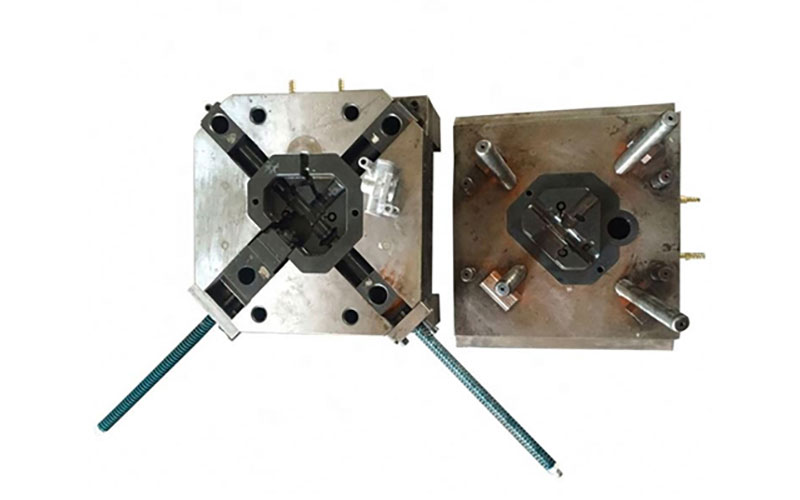
Production molds are the most common type of die casting molds and can be used for mass production. They are manufactured from high-quality, durable materials to ensure longer mold life.
- 1-to-1 Quote Analysis
- Direct Delivery to You
- Fast Production Cycle Times
- High Strength and Hardness
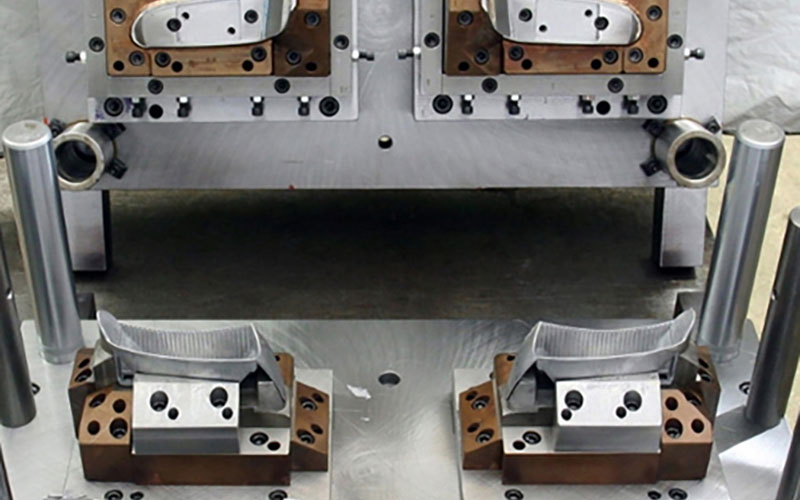
After the casting is completed, the parts will produce casting residues such as sprues, runners, risers, and flash. Trimming dies are used to cut excess material from finished die castings. It is also used to separate parts from casting models. Trimming molds can also be used for mass production and production molds
- 100% Part Inspection
- Good Corrosion Resistance
- High Precision & Efficiency
- No minimum order quantity
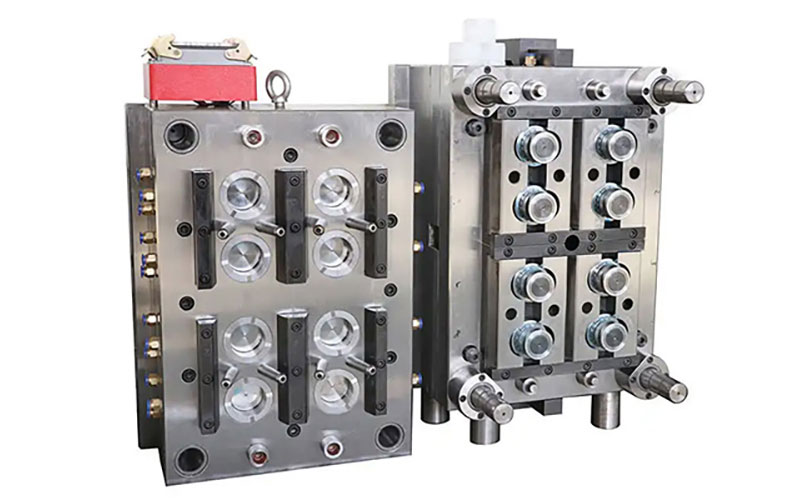
Unit Die Casting Molds are a cost-effective alternative to conventional molds. Unit molds use common parts and are used for low-volume and less complex parts. Custom molds are more effective for high-volume parts with complex geometries. These molds are specifically designed for the part to provide maximum control and efficiency.
- Fast Turnaround
- 1-to-1 Quote Analysis
- Competitive & Affordable Price
- State-of-the-art Equipment
Our Robust Die Casting Mold Making Capabilities
From Prototyping to Manufacturing
NOBLE is your trusted one-stop custom manufacturing solution, from prototype design to manufacturing, through huge manufacturing resources, suitable technology, streamlined process, expert guidance, and perfect quality inspection process to turn your ideas into reality.
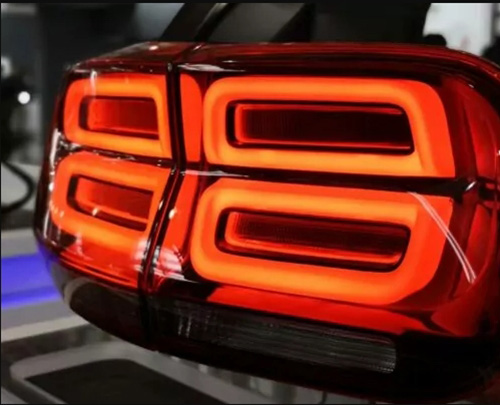
Prototype Machining
From NOBLE, get an online quote with free design analysis in hours to get your CNC machined prototypes done in days.
- State-of-the-art Equipment
- 10+ Years of CNC Machining
- Competitive & Affordable Price
- Quote Within 24 hours
- Free DFM Feedback
- Fast Turnaround in 7 days
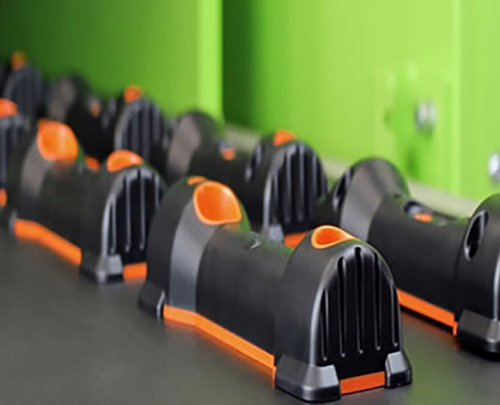
Low-Volume Manufacturing
With advanced production equipment and an experienced team of engineers, we can manufacture products with complex geometric shapes and high precision requirements with strict tolerance control and perfect quality inspection processes.
- Competitive & Affordable Price
- State-of-the-art Equipment
- 10+ Years of Low-Volume Manufacturing
- Fast Lead Time
- 30+ Countries shipped
- 100% Part Inspection
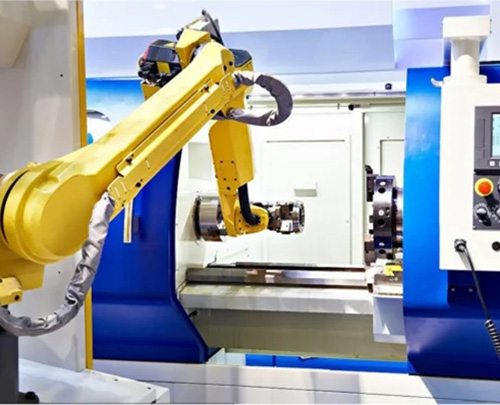
Medium & Mass Production
NOBLE meets mass production needs through strict tolerance control, quality inspection, and a complete supply chain, and quickly delivers cost-effective, high-precision parts.
- 10+ Years of Medium&Mass Production
- Competitive & Affordable Price
- Large Supplier Network
- 100,0000+ Unique parts produced
- Guaranteed Consistent Quality
- Fast Turn-Around Production
Why Choose Us for Custom Die Casting Mold Making Services
Providing high-precision and long-life die-casting mold services at competitive prices, combining cutting-edge die-casting mold technology with advanced production equipment, our expert engineers are dedicated to reducing cycle times by up to 50%+, with fast turnaround, obtaining in minutes Get a quote and getting your die casting mold within days.
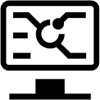
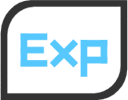
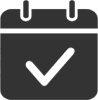
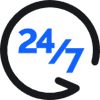
Work with Us in 4 Simple Steps Only
With many years of manufacturing experience, NOBLE offers the best solutions for all rapid prototyping and low-volume manufacturing needs. We streamline the innovation cycle into four simple but effective steps.



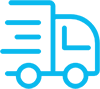
Die Casting Mold Making Tolerances and Standards
Dimension | Standards |
Size Tolerance | ±0.01mm |
Geometric Tolerance | ±0.05mm |
Surface roughness | Ra0.8μm |
Hardness | 48-52HRC |
Material | A380、A383(ADC12)、A413 |
Materials for Custom Die Casting Mold Making Parts
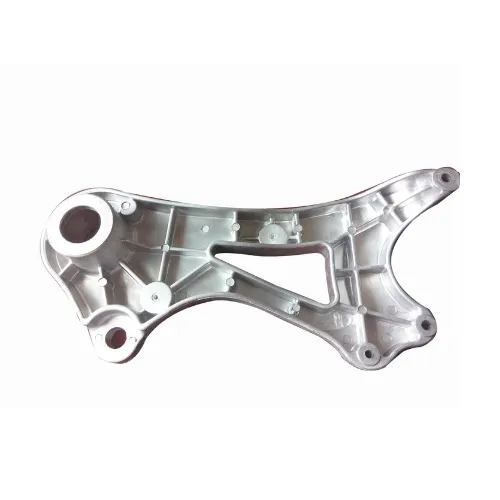
Aluminum
- 1202-1292°F melting temperature
- Used Y10 and HM3 steel-grades
- Focus on dry cracking & sticking
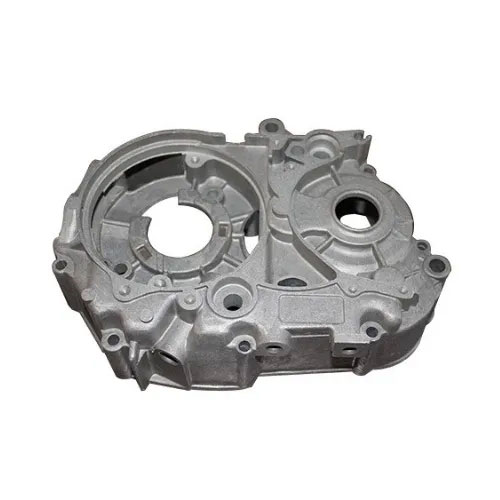
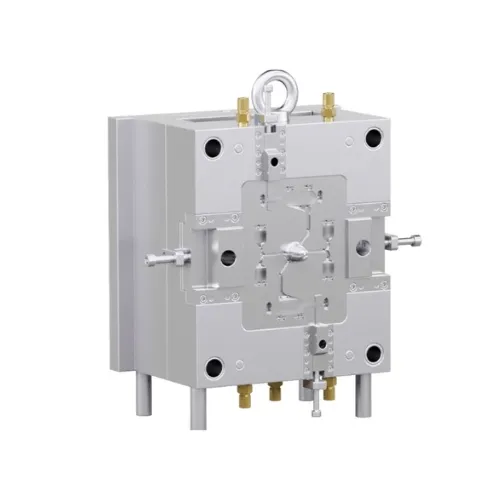
Surface Finishes for CNC Machining
CNC machining leaves visible tool marks during the process of removing portions of the block’s surface to create desired shapes. If you don’t want as-machined parts, select a surface finishing for your custom parts. At NOBLE, we offer several common surface finishes that help improve functionality and aesthetics.
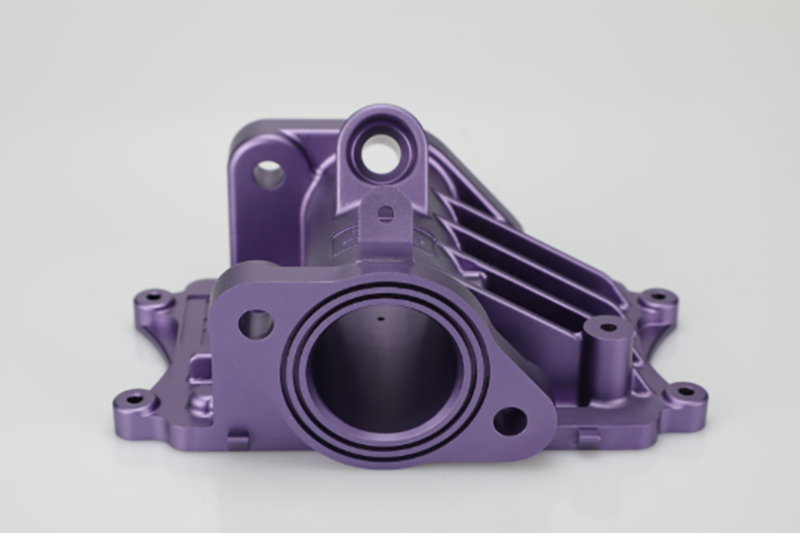
Anodizing
Anodizing improves corrosion resistance, enhancing wear resistance and hardness, and protecting the metal surface. Widely used in mechanical parts, aircraft, and automobile parts, precision instruments, etc.
Materials: Aluminum
Color: Clear, black, grey, red, blue, gold.
Texture: Smooth, matte finish
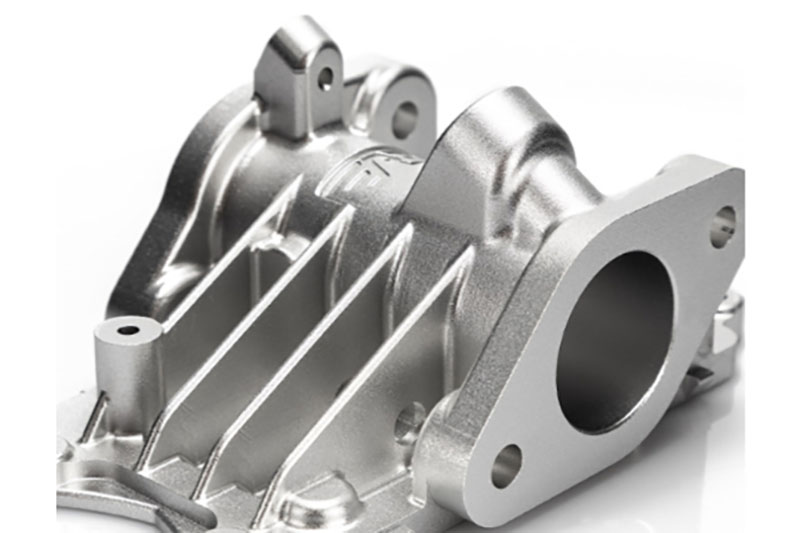
Sand Blasting
Sand blasting results in parts with a smooth surface with a matte texture. Used mainly for visual applications and can be followed by other surface treatments.
Materials: ABS, Aluminum, Brass
Color: N/A
Texture: Matte
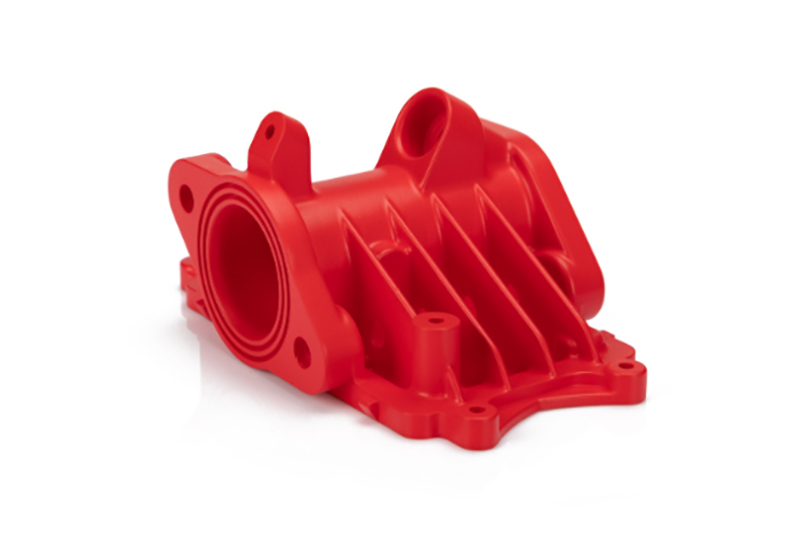
Powder Coating
Powder coating is a type of coating that is applied as a free-flowing, dry powder. Unlike conventional liquid paint which is delivered via an evaporating solvent, powder coating is typically applied electrostatically and then cured under heat or with ultraviolet light.
Materials: Aluminum, Stainless Steel, Steel
Color: Black, any RAL code or Pantone number
Texture: Gloss or semi-gloss
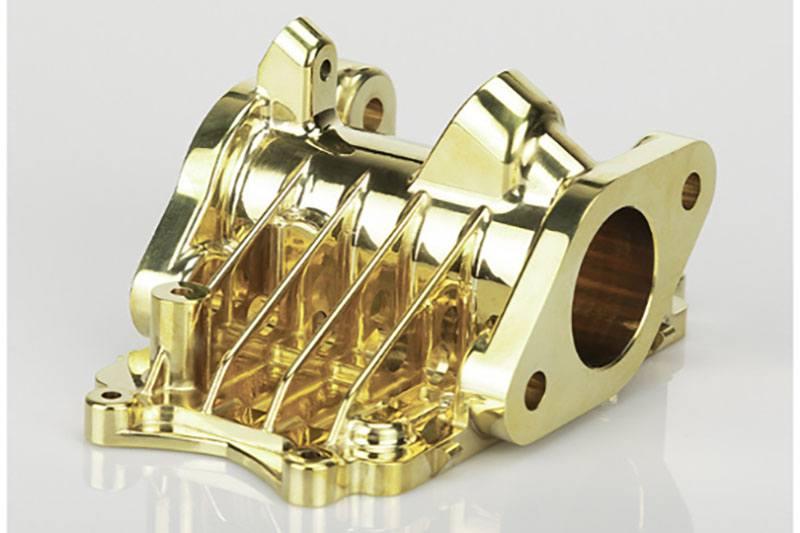
Electroplating
Electroplating can be functional, decorative or corrosion-related. Many industries use the process, including the automotive sector, in which chrome-plating of steel automobile parts is common.
Materials: Aluminum, steel, Stainless Steel
Color: N/A
Texture: Smooth, Glossy finish
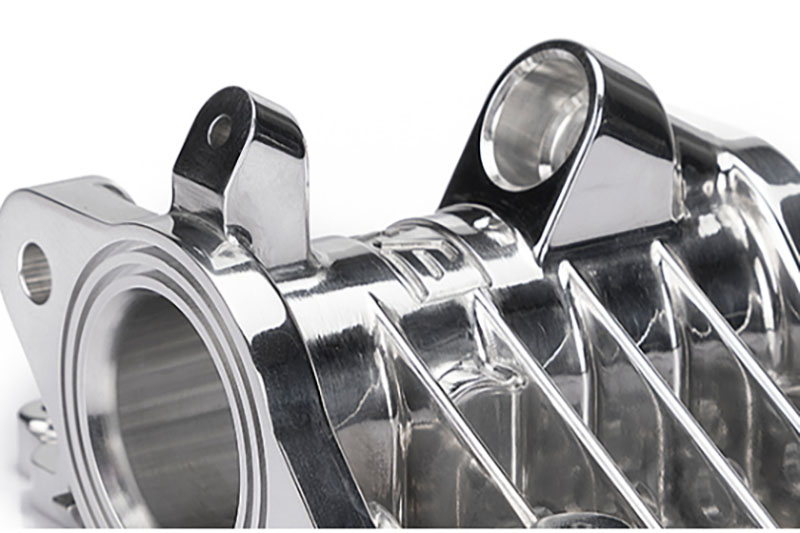
Polishing
Polishing is the process of creating a smooth and shiny surface, either through physical rubbing of the part or by chemical interference. The process produces a surface with significant specular reflection, but in some materials is able to reduce diffuse reflection.
Materials: Aluminum, Brass, Stainless Steel, Steel
Color: N/A
Texture: Glossy
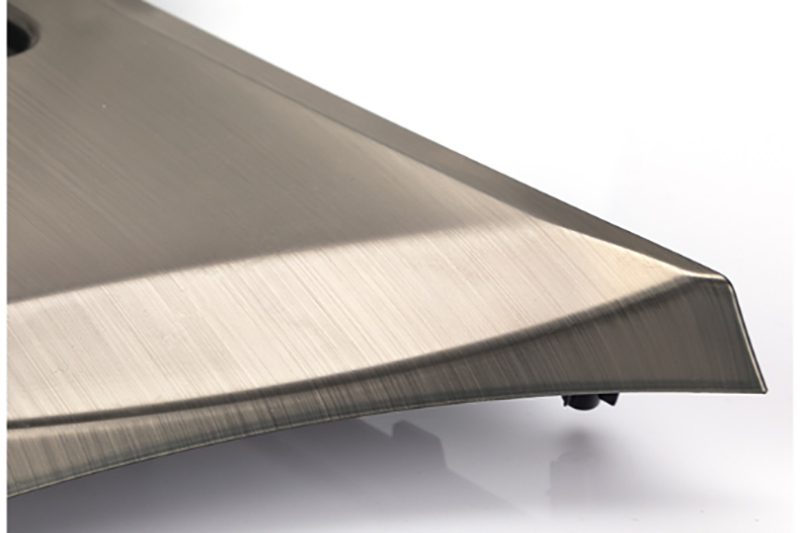
Brushing
Brushing is a surface treatment process in which abrasive belts are used to draw traces on the surface of a material, usually for aesthetic purposes.
Materials: ABS, Aluminum, Brass, Stainless Steel, Steel
Color: N/A
Texture: Satin
Custom Die Casting Mold Making Parts Display
Please browse through our extensive gallery showcasing precision die casting mold making created by our esteemed customers.
See What Our Customers Say About Us
The feedback of customers has a greater impact than a company’s advertising. Take a look at what our satisfied customers have to say about how we met their needs.
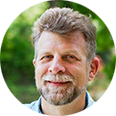
Emily
Project Engineer
NOBLE die castina’s mold services have been instrumental in our success. Their attention to detail and ability tohandle complex desians have resulted in precise and durable components for our medical eauioment. Their professionalism and commitment to customer satisfaction are unparalleled.
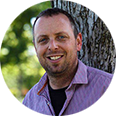
John
Automotive Engineer
The die casting mold services provided by NOBLE exceeded our expectations. They delivered high-quality moldsthat allowed us to achieve precise and consistent parts. Their expertise and attention to detail ensured efficientproduction and cost savings.
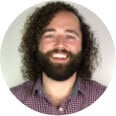
Sarah
Aerospace Engineer
We have been relying on NOBLE die casting for our mold needs for years. Their experienced team consistentlydelivers molds that meet our stringent requirements. Their exceptional quality, reliability, and on-time delivery havemade them our trusted partnerin the aerospace industry.
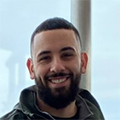
Mark
Senior Engineer
The die castina molds provided by NOBLE have sianificantly improved our production process. With their molds, weachieved excellent part quality, reduced scrap rates, and increased productivity. Their knowledgeable team guidedus throughout the process,ensuring successful outcomes.
What is Die Casting Mold?
A die-casting mold is made up of two parts: the stationary (fixed) and the moveable (ejector) mold halves. The ejector dies half, which houses the casting ejector, is fixed to the moveable fixing plate and is mounted to the fixed fixing plate of the die casting machine. The two mold halves are closed when casting is ready, and the die-locking force on the machine keeps them closed. The mold parting, also known as the mold parting plane, is the surface that makes contact between the two mold halves. The ejector die half is the sole part that is subject to the opening and closing actions. By using manually or hydraulically powered core slides (cores), cavities or undercuts are de-molded.
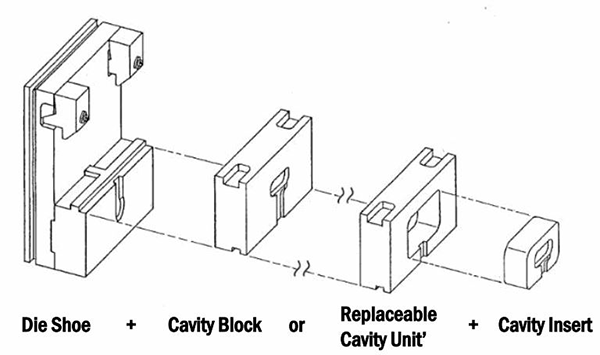
Die Casting Mold Making Applications
NOBLE is committed to providing cutting-edge manufacturing solutions to satisfy the various needs of our customers. Our major objective is to offer consumers in many sectors high-quality products at affordable costs. Our devoted crew is well-equipped to meet a variety of industrial requirements. Here are some typical industries that we work with.

Oil & Gas
Die casting molds are employed in the oil and gas industry to manufacture critical components such as valves, fittings, connectors, and pump parts. Die casting offers the advantage of producing high-strength and corrosion-resistant components required for challenging environments in the oil and gas sector.
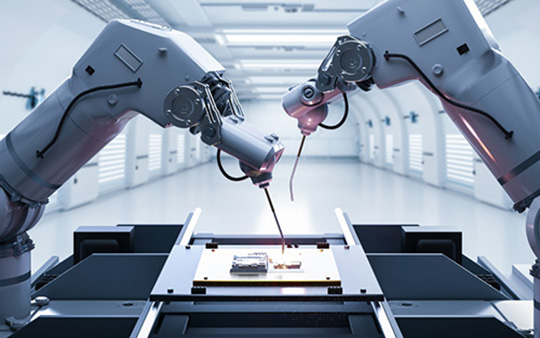
Automation Equipment
NOBLE Rapid Prototyping service allows you to quickly and easily create automated functional prototypes to test and optimize your design, select the right process, reduce costs, and shorten project cycles. On-demand services can produce automated parts with a high level of accuracy.
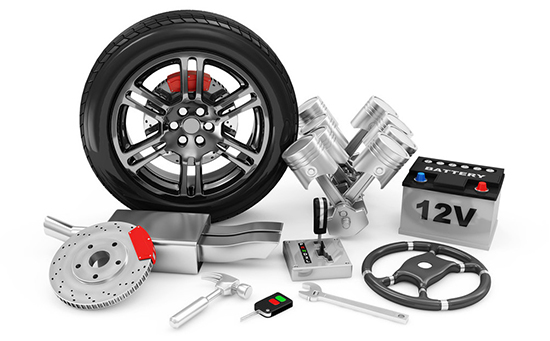
Automotive
Our die casting mold making services enables the production of a wide range of components that contribute to the performance, safety of vehicles in the automotive industry. Components like engine blocks, transmission cases, cylinder heads, and various structural parts.
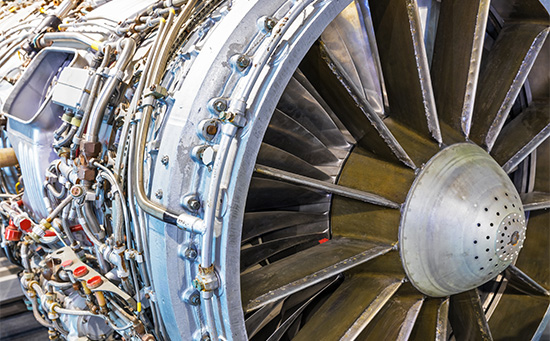
Aerospace
The experts at NOBLE have in-depth knowledge of die casting mold making methods for the aerospace sector. Utilize our die casting mold making capabilities to create lightweight, highly durable components without sacrificing strict aviation standards.
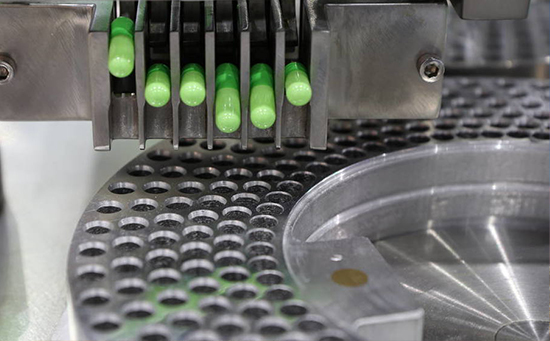
Medical Devices
Die casting molds are utilized in the medical industry to produce precise and complex components like surgical instruments, implantable devices, and diagnostic equipment parts. The high accuracy, repeatability, and cost-effectiveness of die casting make it suitable for meeting the stringent requirements of the medical sector.
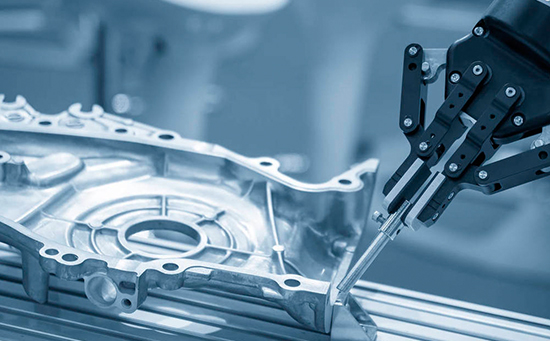
Robotics
Our cutting-edge capabilities, innovative craftsmanship, and skilled engineering team could better serve the robotics field with advanced die casting mold making solutions.
If you are looking for a rapid prototyping manufacturer or a CNC machine shop to fabricate small, medium-volume, or mass-production products, NOBLE is an ideal choice.Our well-trained and experienced staff manufactures parts in line with drawings on modern CNC machines, with the highest accuracy and processing quality in all sizes.In addition, we provide professional design considerations for your CNC machining projects.
Want to get the most professional and fastest service for your CNC machining project? Upload your CAD files now and obtain a quote!
Die Casting Mold Making FAQs
In die casting, different types of molds are used, including steel molds, also known as dies. These dies are typically made from hardened steel and consist of two halves, the “fixed half” and the “movable half.” The fixed half remains stationary, while the movable half is attached to the die casting machine and opens and closes during the casting process. The molds are precision-engineered to create the desired shape and intricacies of the final product. The choice of mold material and design depends on factors such as the casting material, complexity of the part, and production volume.
Aluminum die-cast toolings are prepared using a variety of methods and materials. It is made using the final object’s template. The material that was utilized to build the molds is visible in the die-cast item. Designing, construction, secondary processing, assembly are main four process.
Creating a die cast mold involves several steps. First, a design for the mold is created, considering factors like part geometry and material. Next, the mold is crafted using high-quality steel or other suitable materials. The mold is precision machined to the desired shape and features. Cooling channels are incorporated to regulate temperature during the casting process. Finally, the mold undergoes surface treatments and finishes to enhance durability and release properties. The process requires expertise in mold design, machining, and surface treatment to ensure optimal performance and quality in die casting production.
Die casting is a process that uses high pressure to force molten metal into a mould. Mold casting is a process that uses gravity to fill a mould with molten metal. Die casting produces parts that are more precise and have a better surface finish than those produced by mould casting.
Aluminium.magnesium,zinc and brass are four common materials for die casting.
Die casting offers several advantages that make it a preferred manufacturing process in certain applications. It allows for the production of complex, intricate, and high-precision parts with tight tolerances. Die casting provides excellent dimensional accuracy and repeatability, resulting in consistent part quality. The process allows for high production rates and cost efficiency, making it suitable for large-scale manufacturing. Additionally, die casting offers excellent material properties, such as high strength and durability. It is often utilized in industries like automotive, aerospace, electronics, and appliances, where these advantages are crucial for efficient and reliable production.
Yes, die casting molds can be reused multiple times. The molds, typically made of high-quality steel, are designed to withstand the high temperatures and pressures involved in the die casting process. After each casting cycle, the mold can be cleaned, inspected, and prepared for the next production run. Proper maintenance and occasional repairs, such as weld repairs or cavity replacements, can extend the lifespan of the mold. Reusing molds in die casting helps optimize production costs and ensures consistent part quality throughout multiple production runs.