Aluminum Die Casting Services
Our Custom Aluminum Die Casting Service
NOBLE provides customized aluminum alloy die-casting solutions according to the specific needs of each customer, from prototype design to manufacturing production, providing customers with high-precision, stable-performance aluminum alloy die-casting parts at competitive prices. Quotation in minutes, delivery in days.
- Advanced Equipment & Cost-Effective Price
- ISO 9001 & ISO13485 Certified Factory
- 10+ Years of Aluminum Die Casting
- Tolerance Down to 0.001mm
- Lead Time As Fast As 3Days
- 24/7 Engineering Support
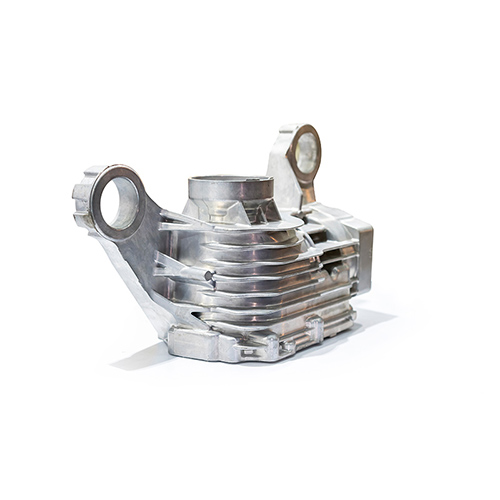
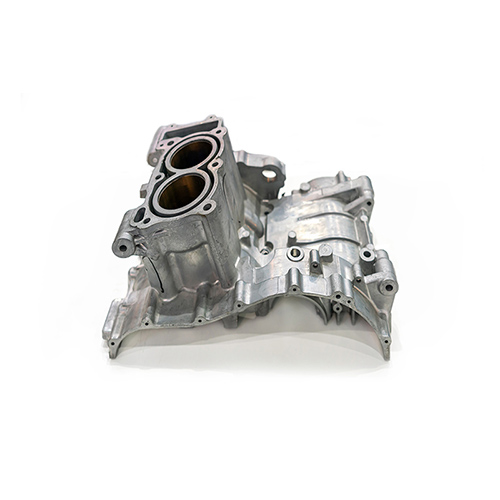
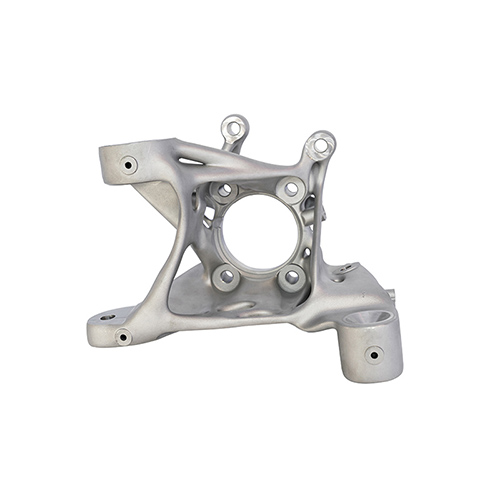
STEP | STP | STL | IGS | IGES | PRT | SLDPRT | SAT | X_T | IPT | CATPART | PDF
Max. file size: ≤20MB
- All uploads are secure and confidential.
Our Powerful CNC Machining Processes
Providing custom CNC machining solutions at competitive prices, we choose from over 100 materials and 60+ surface finishes to ensure you receive high-precision, structurally complex, and performance-stable parts. Try our precision CNC machining services and become our next satisfied customer.
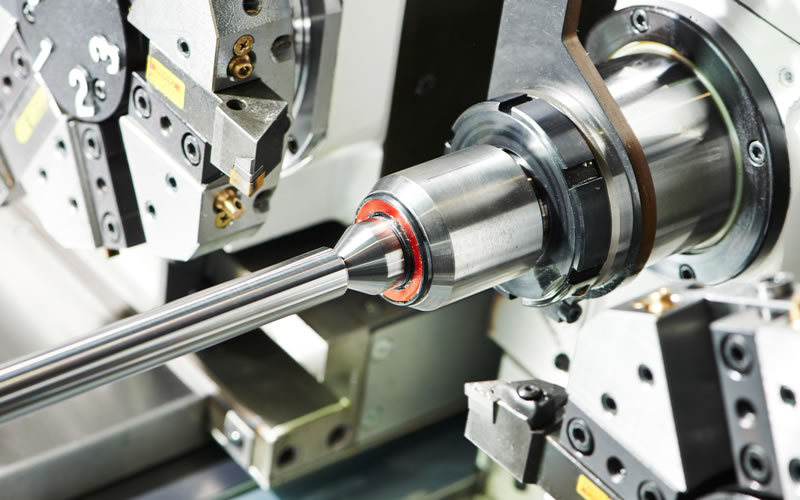
CNC turning is the process of cutting metal or plastic parts with cylindrical features from the outside of a bar with a rotating tool. The turning process can effectively manufacture circular parts and can be applied to create parts with complex internal and external geometries and various threads.
- Tolerances Down to ± 0.0003 In.
- Competitive Price 30% Cost Save
- Fast Turnaround in 7 days
- Quick Turn Milling Services
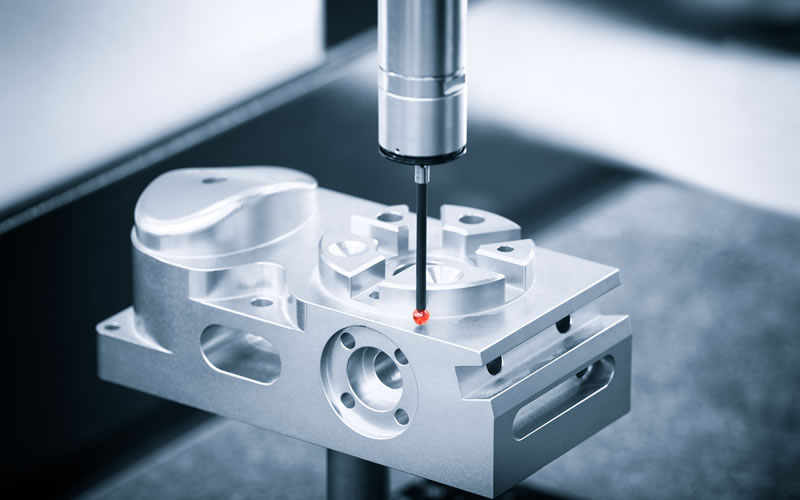
CNC milling is a subtractive process that uses 3-, 4-, and 5-axis milling machines and a variety of cutting tools to remove material from solid blocks of plastic and metal into final parts with varying geometries. With our 3-axis and 5-axis CNC milling services, you will be able to get milled parts with a tolerance of 0. 01mm.
- Tolerances Down to ± 0.0002 In.
- Quote Within 24 hours
- Fast Turnaround in 7 days
- Quick Turn Turning Services
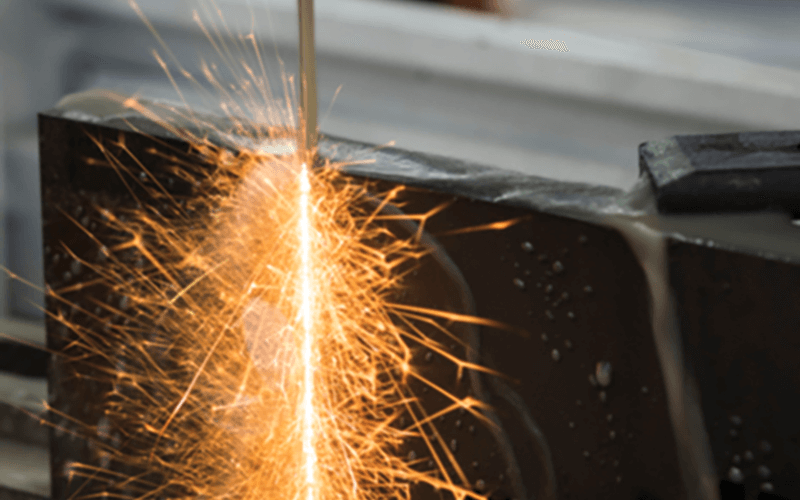
EDM and wire-cutting are CNC machining processes that use copper, graphite, or molybdenum wire to get the desired design for undercuts, sharp corners, and the removal of unnecessary material from workpieces. EDM is also frequently used to produce mold and rapid tooling.
- State-of-the-art Equipment
- 10+ Years of EDM & Wire-Cut
- Fast Turnaround in 7 days
- 1-to-1 Quote Analysis
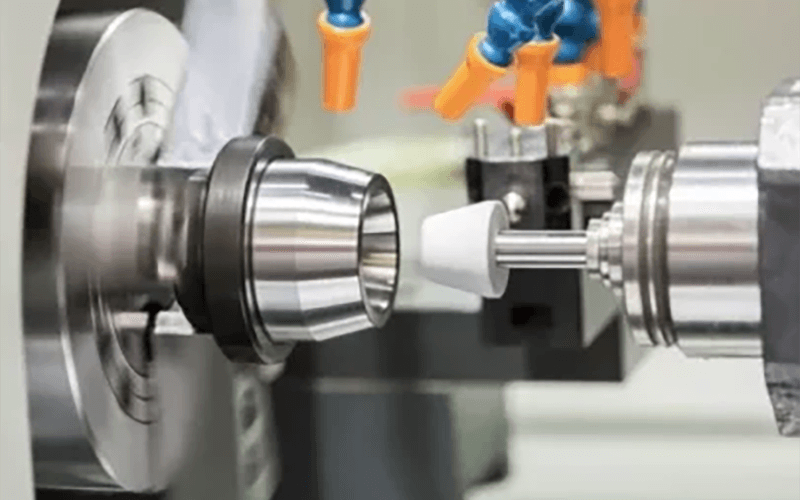
Our CNC grinding machining service will be your best option if you need a very flat surface item or a round part with tolerances of OD and ID ±0.005mm for your production demands.
- Tolerances Down to ± 0.0005 mm.
- Competitive Price 30% Cost Save
- Fast Turnaround in 7 days
- Quick Turn Grinding Services.
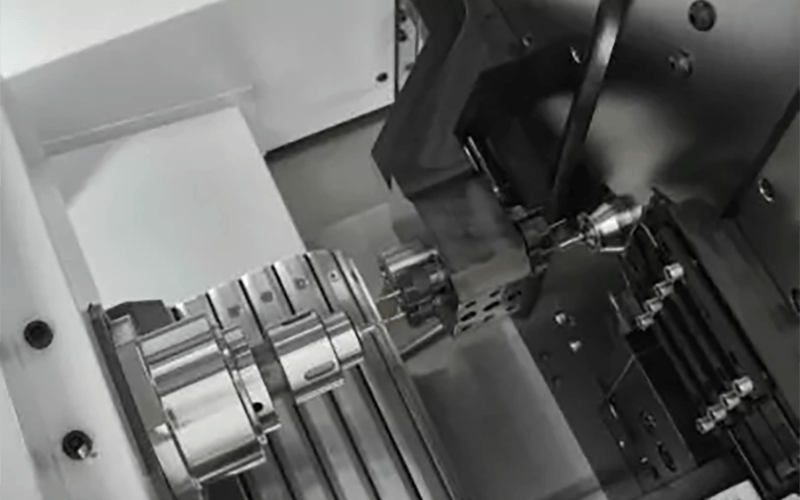
Swiss machining is a productive method for creating thin or complex parts. We can always cut the material that is near the workpiece holder by moving the workpiece as well as the active tooling. To prevent distortion in contrast to a conventional CNC lathe.
- Tolerances Down to ± 0.0005 mm.
- Competitive Price 30% Cost Save
- Fast Turnaround in 7 days
- Quick Turn Swiss Machining Services.
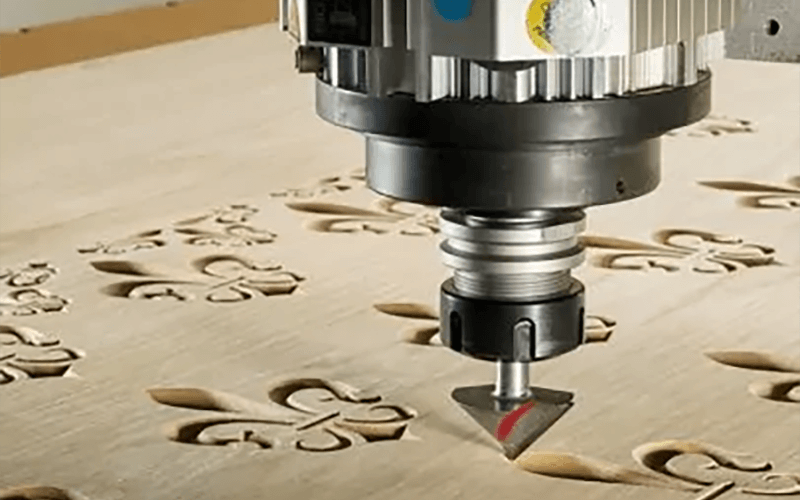
We provide CNC routing services for prototypes and parts machining of soft materials like EPS foam, EVA, and wood in addition to regular milling services for parts made of engineering plastics or metals.
- 10+ Years of CNC Routing
- Competitive & Affordable Price
- 100% Part Inspection
- Fast Turnaround in 7 days
Our Robust Aluminum Die Casting Capabilities
From Prototyping to Manufacturing
NOBLE is your trusted one-stop custom manufacturing solution, from prototype design to manufacturing, through huge manufacturing resources, suitable technology, streamlined process, expert guidance, and perfect quality inspection process to turn your ideas into reality.
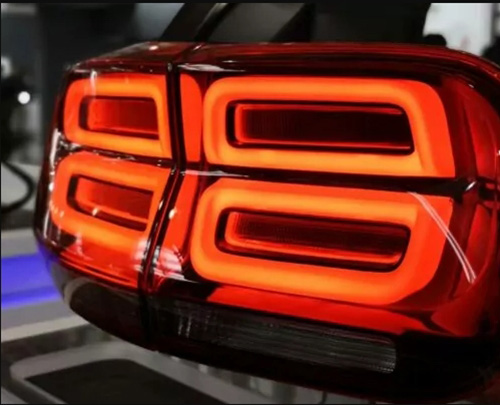
Prototype Machining
From NOBLE, get an online quote with free design analysis in hours to get your CNC machined prototypes done in days.
- State-of-the-art Equipment
- 10+ Years of CNC Machining
- Competitive & Affordable Price
- Quote Within 24 hours
- Free DFM Feedback
- Fast Turnaround in 7 days
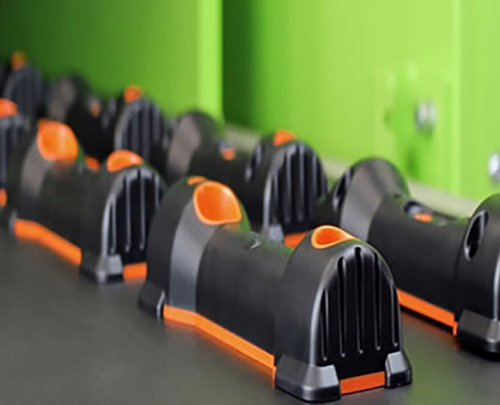
Low-Volume Manufacturing
With advanced production equipment and an experienced team of engineers, we can manufacture products with complex geometric shapes and high precision requirements with strict tolerance control and perfect quality inspection processes.
- Competitive & Affordable Price
- State-of-the-art Equipment
- 10+ Years of Low-Volume Manufacturing
- Fast Lead Time
- 30+ Countries shipped
- 100% Part Inspection
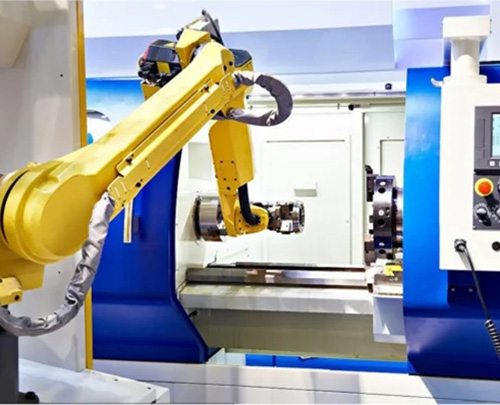
Medium & Mass Production
NOBLE meets mass production needs through strict tolerance control, quality inspection, and a complete supply chain, and quickly delivers cost-effective, high-precision parts.
- 10+ Years of Medium&Mass Production
- Competitive & Affordable Price
- Large Supplier Network
- 100,0000+ Unique parts produced
- Guaranteed Consistent Quality
- Fast Turn-Around Production
Why Choose Us for Custom Aluminum Die Casting Services
NOBLE prioritizes our customers and uses cutting-edge technology and skilled experts to provide precise, efficient, cost-effective, flawless aluminum die casting services that can help propel your business beyond success.
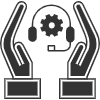
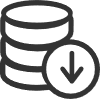
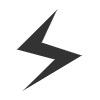
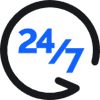
Work with Us in 4 Simple Steps Only
With many years of manufacturing experience, NOBLE offers the best solutions for all rapid prototyping and low-volume manufacturing needs. We streamline the innovation cycle into four simple but effective steps.



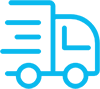
Aluminum Die Casting Advantages
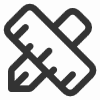
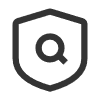
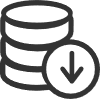
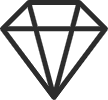
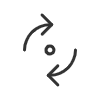
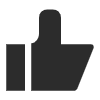
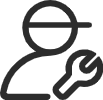
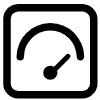
Aluminum Die Casting Tolerances and Standards
NOBLE specialises in aluminum die casting and custom aluminum die casting with a wide range of sizes and surface finishes. Contact us and give us your drawings for a one-stop aluminum casting service.
Standard | Capabilities |
Casting Size (mm) | 10-1000 |
Maximum Casting Weight (kg) | 10 |
Minimum Wall Thickness (mm) | 0.5 |
Tolerance (mm) | 0.02 |
Surface Finish | Ra1.6 |
Tolerance | CT4-CT7 |
MOQ | NO MOQ |
Additional Services | CNC machining, Powder coating, Anodizing, Assembly, Packaging, etc. |
Materials for Custom Aluminum Die Casting
The qualities of cast aluminum alloys vary depending on the alloy composition and manufacturing factors. Some general features of common cast aluminum alloys are as follows:
360 360.0 | A360 A360.0 | 380 380.0 | A380 A380.0 | 383 383.0 | |
Density | 2.63 g/cm3 | 2.63 g/cm3 | 2.74 g/cm3 | 2.71 g/cm3 | 2.74 g/cm3 |
Melting Range | 557-596.C | 557-596.C | 540-595.C | 540-595.C | 516-582.C |
Electrical Conductivity | 30 %IACS | 29 %IACS | 27 %IACS | 23 %IACS | 23 %IACS |
Thermal Conductivity | 113 W/(m’ K) | 113 W/(m’ K) | 96.2 W/(m’ K) | 96.2 W/(m’ K) | 96.2 W/(m’ K) |
Ultimate Tensile Strenghth | 300 MPa | 320 MRa | 320 MRa | 320 MRa | 310 MRa |
Yield Strength | 170 MPa | 170 MPa | 170 MPa | 170 MPa | 170 MPa |
Hardness | 75 BHN | 75 BHN | 75 BHN | 75 BHN | 75 BHN |
Fatigue Strength | 140 MPa | 140 MPa | 140 MPa | 140 MPa | 140 MPa |
Shear Strength | 190 MPa | 190 MPa | 190 MPa | 190 MPa | 190 MPa |
Elongation | 2.5% | 2.5% | 2.5% | 2.5% | 2.5% |
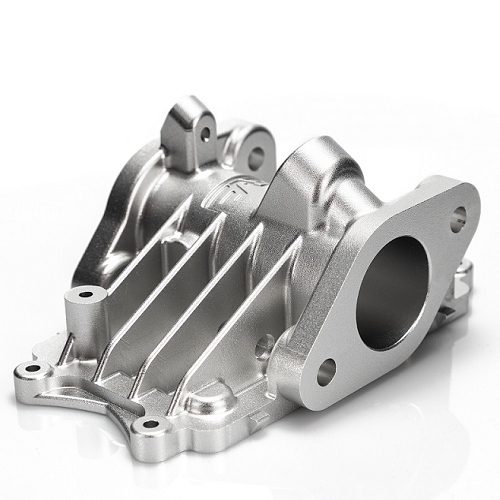
Aluminum
Aluminum is a highly ductile metal, making it easy to machining. The material has a good strength-to-weight ratio and is available in many types for a range of applications.
Price: $
Lead Time: 3 days
Tolerances: ±0. 01mm
Max part size: 200 x 80 x 100 cm
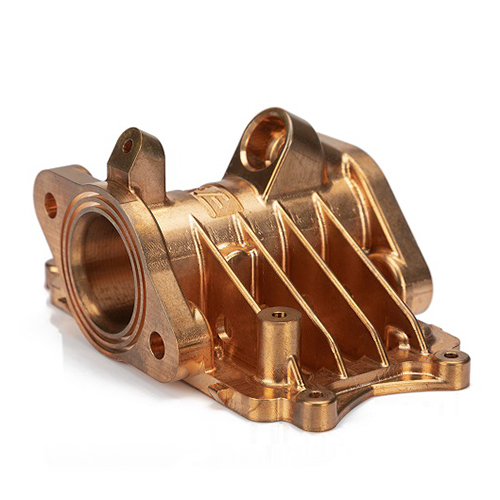
Copper
Copper displays excellent thermal conductivity, electrical conductivity and plasticity. It is also highly ductile, corrosion resistant and can be easily welded.
Wall Thickness: 0. 75 mm
Lead Time: 3 days
Tolerances: ±0. 01mm
Max part size: 200 x 80 x 100 cm
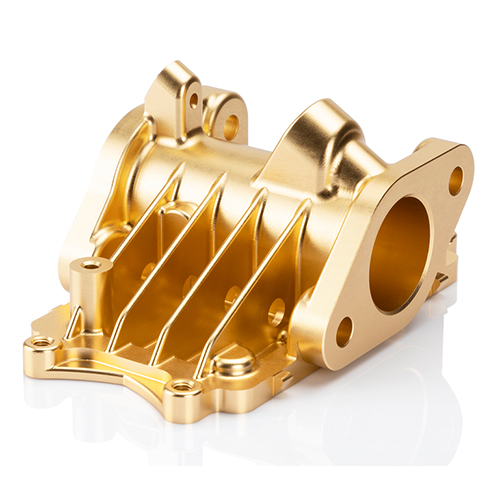
Brass
Brass has desirable properties for a number of applications. It is low friction, has excellent electrical conductivity and has a golden (brass) appearance.
Wall Thickness: 0. 75 mm
Lead Time: 3 days
Tolerances: ±0. 01mm
Max part size: 200 x 80 x 100 cm
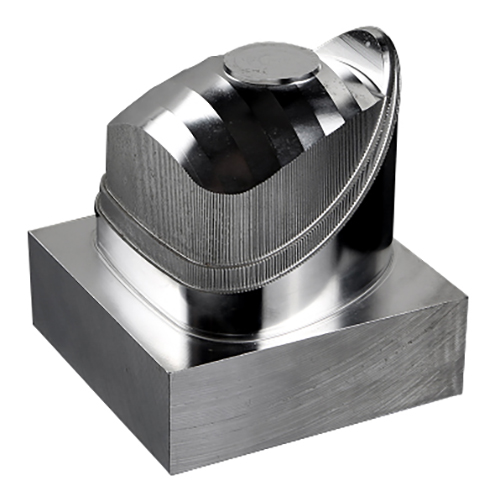
Stainless Steel
Stainless steel is the low carbon steel that offers many properties that are sought after for industrial applications. Stainless steel typically contains a minimum of 10% chromium by weight.
Wall Thickness: 0. 75 mm
Lead Time: 3 days
Tolerances: ±0. 01mm
Max part size: 200 x 80 x 100 cm
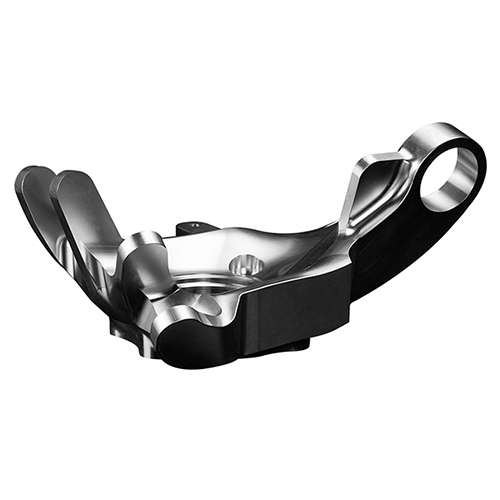
Titanium
Titanium has a number of material properties that make it the ideal metal for demanding applications. These properties include excellent resistance to corrosion, chemicals and extreme temperatures. The metal also has an excellent strength-to-weight ratio.
Wall Thickness: 0. 75 mm
Lead Time: 3 days
Tolerances: ±0. 01mm
Max part size: 200 x 80 x 100 cm
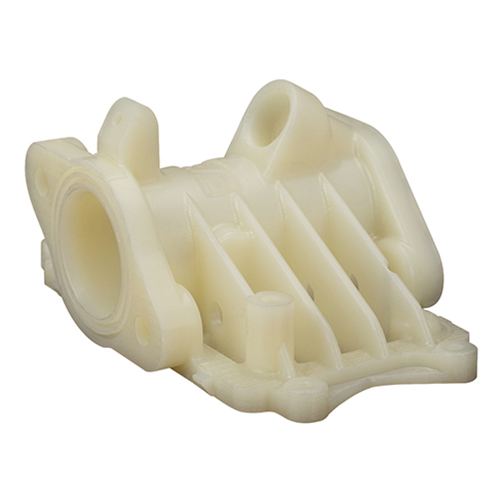
Plastics
Plastics are also a very popular option for CNC machining because of its wide choices, relatively lower price, and significantly faster machining time needed. We provide all common plastics for CNC machining services.
Machinable Material Types: POM, HDPE, PET, Nylon, PTFE, PVC,
Lead Time: 3 days
Tolerances: ±0. 01mm
Max part size: 200 x 80 x 100 cm
Surface Finishes for Aluminum Die Casting
NOBLE offers customizable surface finishes that elevate your product’s appearance, resistance, and quality beyond expectations. Our finishes cover tool marks and enhance hardness, roughness, and corrosion resistance. Explore our options for flawless results.
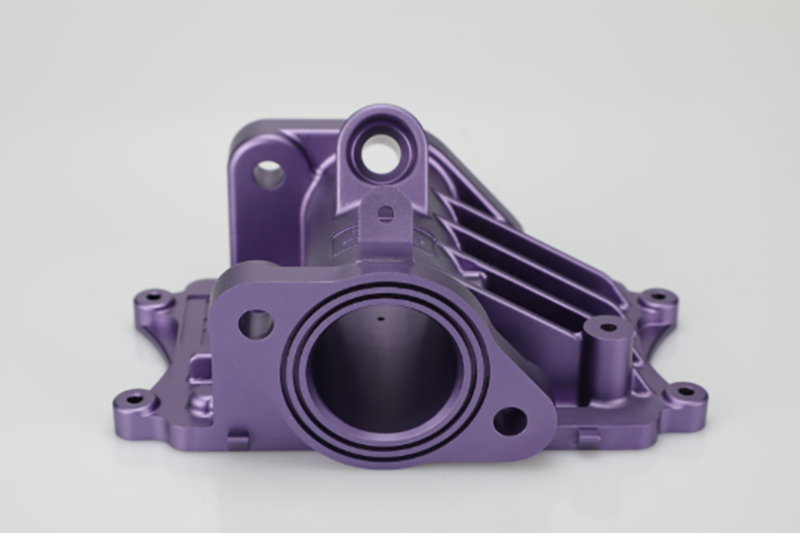
Anodizing
Anodizing improves corrosion resistance, enhancing wear resistance and hardness, and protecting the metal surface. Widely used in mechanical parts, aircraft, and automobile parts, precision instruments, etc.
Materials: Aluminum
Color: Clear, black, grey, red, blue, gold.
Texture: Smooth, matte finish
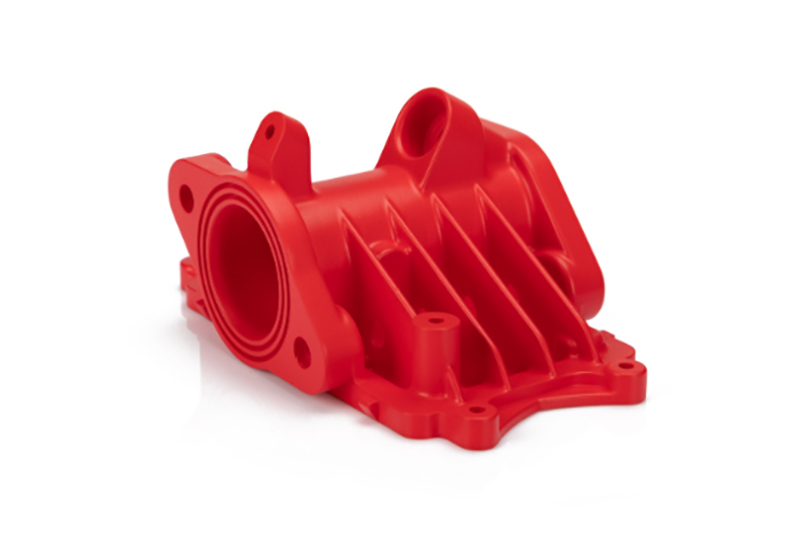
Powder Coating
Powder coating is a type of coating that is applied as a free-flowing, dry powder. Unlike conventional liquid paint which is delivered via an evaporating solvent, powder coating is typically applied electrostatically and then cured under heat or with ultraviolet light.
Materials: Aluminum, Stainless Steel, Steel
Color: Black, any RAL code or Pantone number
Texture: Gloss or semi-gloss
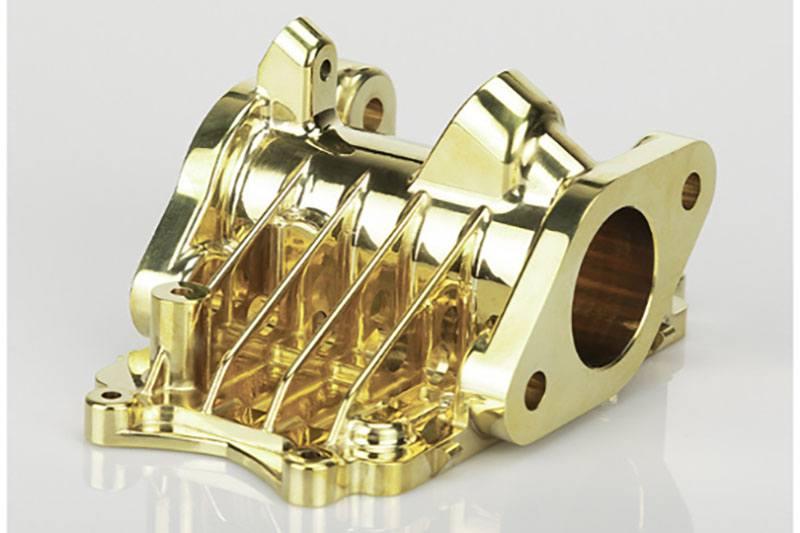
Electroplating
Electroplating can be functional, decorative or corrosion-related. Many industries use the process, including the automotive sector, in which chrome-plating of steel automobile parts is common.
Materials: Aluminum, steel, Stainless Steel
Color: N/A
Texture: Smooth, Glossy finish
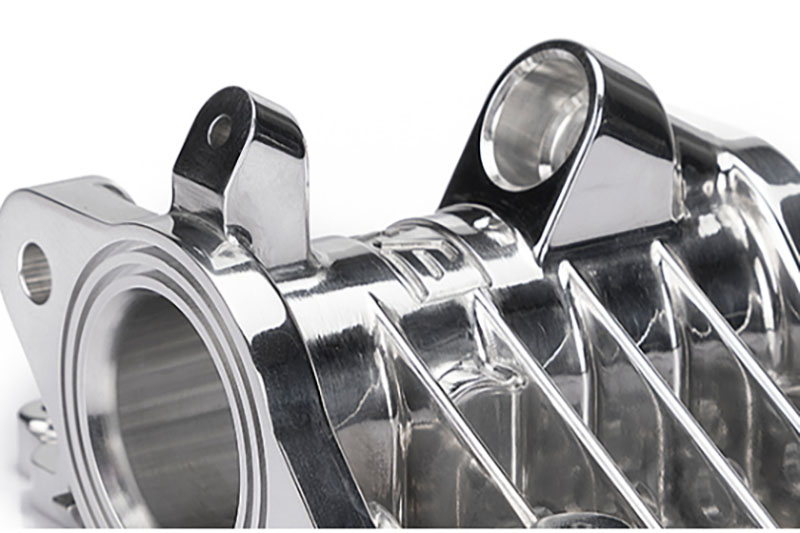
Polishing
Polishing is the process of creating a smooth and shiny surface, either through physical rubbing of the part or by chemical interference. The process produces a surface with significant specular reflection, but in some materials is able to reduce diffuse reflection.
Materials: Aluminum, Brass, Stainless Steel, Steel
Color: N/A
Texture: Glossy
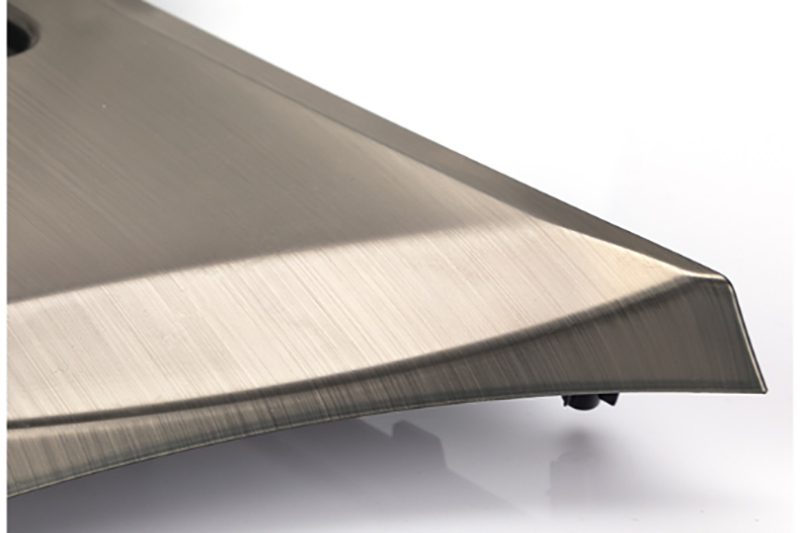
Brushing
Brushing is a surface treatment process in which abrasive belts are used to draw traces on the surface of a material, usually for aesthetic purposes.
Materials: ABS, Aluminum, Brass, Stainless Steel, Steel
Color: N/A
Texture: Satin
Custom Aluminum Die Casting Parts Display
Take a look at our comprehensive parts gallery featuring aluminum die casting made for our valuable customers.
Cold Chamber Aluminum Die Casting Process Workflow
As a premier die casting manufacturer, offers the cold chamber aluminum die casting technique, which is a manufacturing process that employs an aluminum cast alloy to make high-quality, high-precision aluminum parts. The following is an overview of the cold chamber aluminum die casting process:
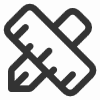
Casting Mold Design
The casting mold, which comprises the mold or dies that will be used to cast the aluminum item, is designed as the first stage in the cold chamber aluminum die casting process.

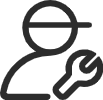
Molten Aluminum Preparation
The next step is to prepare the molten aluminum. This involves melting the aluminum in a furnace at a temperature of around 700-750°C.

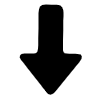
Injection
When the molten aluminum is ready, it is pumped into a separate injection cylinder, sometimes known as a cold chamber, and driven into the steel mold or die. Pressure and temperature are carefully managed to ensure that the aluminum completely fills the mold and hardens promptly.

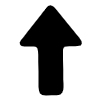
Ejection
When the aluminum has solidified, the mold is opened and the part is ejected.

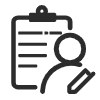
Finishing
Finishing the item is the final step in the cold chamber aluminum die casting process. Trimming superfluous material, eliminating surface flaws, and adding any necessary coatings or finishes are all examples of this.

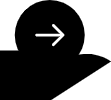
Quality Inspection and Delivery
As a renowned aluminum mold casting factory, NOBLE inspects every aluminum die casting thoroughly. We employ the PDCA approach to continuously enhance the casting production process and ensure that every aluminum mold casting part received by clients is of exceptional quality.
See What Our Customers Say About Us
The feedback of customers has a greater impact than a company’s advertising. Take a look at what our satisfied customers have to say about how we met their needs.
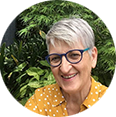
Sarah Patel
Engineering Manager
Working with NOBLE, a manufacturer experienced in aluminum die casting has been a game-changer for ourbusiness. The quick turnaround time and consistent quality of the parts have significantly improved our production efficiency. The strenath-to-weicht ratio of the aluminum parts is remarkable, allowing us to achieve optimal performance in our products. We’re extremely satisfed with the results.
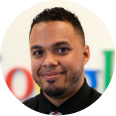
Michael Ramirez
Product Designer
I was amazed by the precision and quality of the aluminum die-cast parts l received from NOBLE. The intricatedetails and smooth finishes exceeded my expectations. The light weight yet durable nature of the components perfectly suited our application, and the cost-effectiveness of the process was an added bonus. Holy recommended!
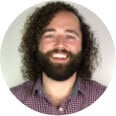
David Johnson
Operations Manager
Choosing NOBLE’s aluminum die casting for our components was an excellent decision. The versatility of the process allowed us to create complex shapes and intricate designs that were not possible with other manufacturing methods. The parts have demonstrated exceptional durability and resistance to corrosion, making them perfect for our demanding industry. The expertise and support provided by the die casting team were instrumental in our success.
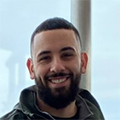
Emily Thompson
CEO
We were initiallv skeptical about switchina to aluminum die-cast parts, but after seeina the results, we couldn’t behappier. The lightweight nature of the components has significantly reduced the overall weight of our products. leading to improved fuel efficiency and enhanced performance. The die-casting process from NOBLE also offereccost savings without compromising on quality. We’re thrilled with the outcome and look forward to continuing our partnership.
Aluminum Die Casting Applications
Aluminum die casting plays an important role in parts manufacturing in automotive, aerospace, electronics, appliances, telecommunications, and medical equipment.
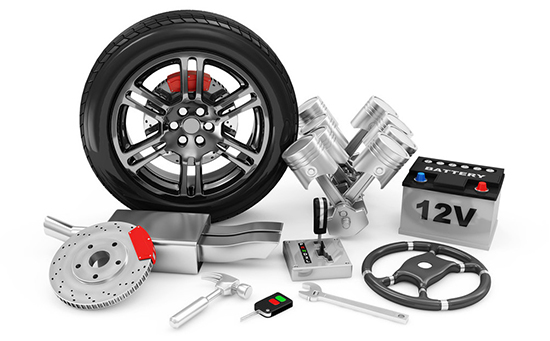
Automotive
Aluminum die casting produces intricate shapes, maintains precise tolerances, and delivers impeccably finished parts. It's an ideal choice for automotive components, such as gears, cylinders, gladhands, and small engine parts.
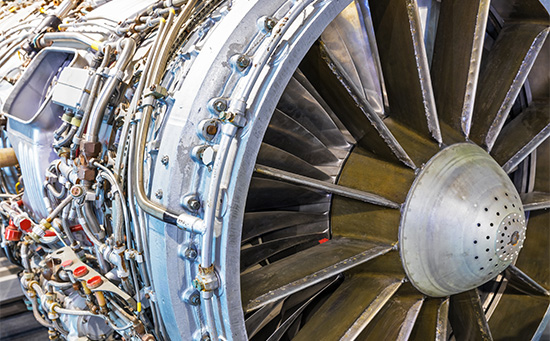
Aerospace
The aerospace industry relies on the essential manufacturing process of aluminum die casting due to its ability to produce complex shapes, maintain tight tolerances, and deliver high-quality finished parts. The lightweight and durable characteristics of aluminum die casting components contribute to improved fuel efficiency, increased payload capacity, and enhanced overall performance of aerospace vehicles.
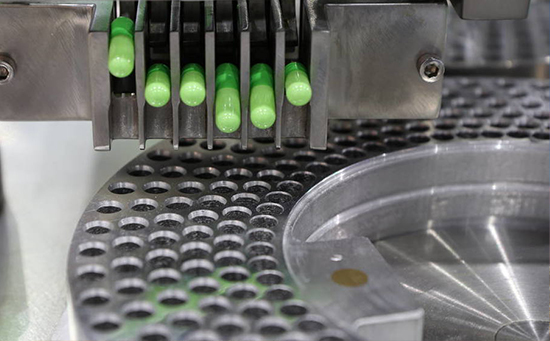
Medical Devices
The safety, functionality, and effectiveness of medical devices and equipment are enhanced by the precise and durable characteristics of aluminum die casting components. Such components are utilized in common medical parts like forceps, clamps, scissors, and retractors.
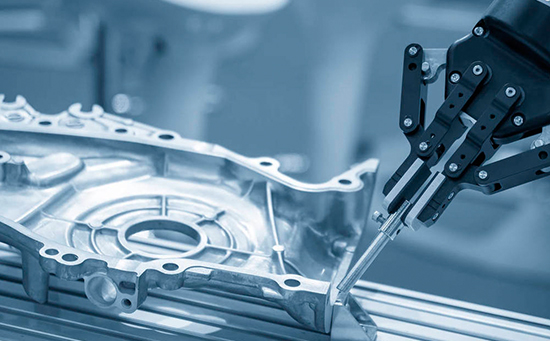
Robotics
Aluminum die casting is advantageous in robotics because it can create intricate shapes and precise results at a cost-efficient price. It's commonly used to produce parts like robot frames, housings, and joints.
If you are looking for a rapid prototyping manufacturer or a CNC machine shop to fabricate small, medium-volume, or mass-production products, NOBLE is an ideal choice.Our well-trained and experienced staff manufactures parts in line with drawings on modern CNC machines, with the highest accuracy and processing quality in all sizes.In addition, we provide professional design considerations for your CNC machining projects.
Want to get the most professional and fastest service for your CNC machining project? Upload your CAD files now and obtain a quote!
Aluminum Die Casting FAQs
Aluminum die casting is a manufacturing method that uses reusable die casting moulds, known as dies, to make geometrically complicated metal parts. A furnace, metal, die casting machine, and die are all used in the die casting process.
Both aluminum casting and die casting have their advantages and are suitable for different applications based on factors such as complexity, production volume, dimensional accuracy, and surface finish requirements. Choosing the appropriate process depends on the specific needs and constraints of the manufacturing project.
Aluminium alloys are used in the majority of die castings produced around the world. The die cast aluminium alloy system is made up of six key elements: silicon, copper, magnesium, iron, manganese, and zinc. Each constituent has an independent and interactive effect on the alloy.
Die casting aluminum offers several key benefits. Firstly, it enables the production of intricate and complex shapes with high precision and tight tolerances. The process ensures excellent dimensional accuracy and surface finish, eliminating the need for extensive post-processing. Die cast aluminum parts are lightweight yet durable, offering a high strength-to-weight ratio. This makes them ideal for applications where weight reduction is crucial, such as in the automotive and aerospace industries. Additionally, die casting is highly efficient for high-volume production, resulting in faster cycle times and cost-effective manufacturing. The versatility, efficiency, and superior mechanical properties of die cast aluminum make it a preferred choice for a wide range of industrial applications.
Die casting.Die casting is the most widely used aluminium casting method for producing aluminium parts. There are two techniques available: low-pressure die casting and high-pressure die casting, with the latter being more appropriate for the material.
Aluminium is noted for its light weight, and cast aluminium is lighter than wrought iron but heavier than tubular frame aluminium.
Aluminium alloy 6061 gravity die castings are used to create intricate shapes that would be too expensive to produce using other technologies. Different casting methods provide the most cost-effective pricing based on quantity, size, material, and other criteria.